Method for efficiently machining tooth-shaped pattern on surface of knob mold
A mold and tooth shape technology, which is applied in the field of high-efficiency processing of the surface tooth pattern of the knob mold, can solve the problems of affecting the appearance and precision of the product, increasing the cumulative error, reducing production efficiency, etc., to avoid time waste and cumulative error, and reduce processing Time, the effect of reducing development and production costs
- Summary
- Abstract
- Description
- Claims
- Application Information
AI Technical Summary
Problems solved by technology
Method used
Image
Examples
Embodiment Construction
[0032] The following will clearly and completely describe the technical solutions in the embodiments of the present invention with reference to the accompanying drawings in the embodiments of the present invention. Obviously, the described embodiments are only some, not all, embodiments of the present invention. Based on the embodiments of the present invention, all other embodiments obtained by persons of ordinary skill in the art without making creative efforts belong to the protection scope of the present invention.
[0033] Such as Figure 2-12 As shown, a method for efficiently processing the tooth pattern on the surface of the knob mold includes the following steps:
[0034] Step 1. Mold design and processing: The mold adopts the dismantling design and includes the mold core 1, insert 2 and slider 3, respectively process the matching insert 2 and slider 3, and process on the mold core 1 The insert hole 11 matched with the insert 2 and the T-shaped groove 12 matched with...
PUM
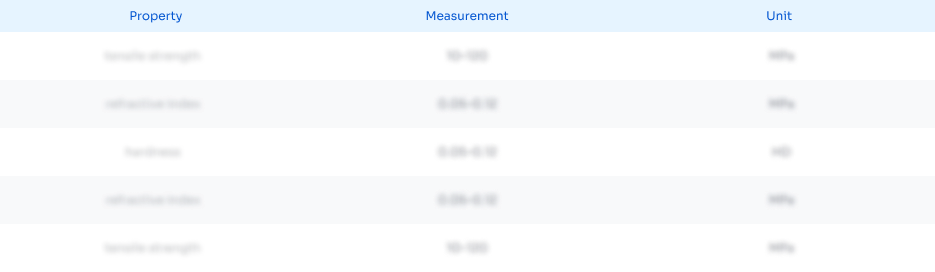
Abstract
Description
Claims
Application Information

- R&D
- Intellectual Property
- Life Sciences
- Materials
- Tech Scout
- Unparalleled Data Quality
- Higher Quality Content
- 60% Fewer Hallucinations
Browse by: Latest US Patents, China's latest patents, Technical Efficacy Thesaurus, Application Domain, Technology Topic, Popular Technical Reports.
© 2025 PatSnap. All rights reserved.Legal|Privacy policy|Modern Slavery Act Transparency Statement|Sitemap|About US| Contact US: help@patsnap.com