Hot tinning device for copper doubled wires
A hot-dip tinning and tinning technology, which is applied in hot-dip plating process, cable/conductor manufacturing, coating, etc., can solve the problems of large production line occupation, long overall process, low tinning efficiency, etc., and achieve the overall process Short length, guaranteed take-up tension, and improved tinning efficiency
- Summary
- Abstract
- Description
- Claims
- Application Information
AI Technical Summary
Problems solved by technology
Method used
Image
Examples
Embodiment Construction
[0031] The preferred embodiments of the present invention will be described in detail below in conjunction with the accompanying drawings, so that the advantages and features of the present invention can be more easily understood by those skilled in the art, so as to define the protection scope of the present invention more clearly.
[0032] like Figure 1 to Figure 4 A preferred embodiment of a copper wire hot-dip tinning device is shown, the hot-dip tinning device includes a wire-releasing mechanism, a cleaning mechanism, a tinning mechanism and a wire-receiving mechanism arranged in sequence from back to front;
[0033] The pay-off mechanism wherein includes a pay-off frame 1, a tensioning guide assembly and a wire distribution plate, and the pay-off frame has a pay-off reel 2; in this embodiment, the pay-off reel 2 is a 630 galvanized iron plate; the pay-off There are bare copper parallel wires containing 8-16 copper monofilaments wound on the reel 2; two pay-off reels 2 a...
PUM
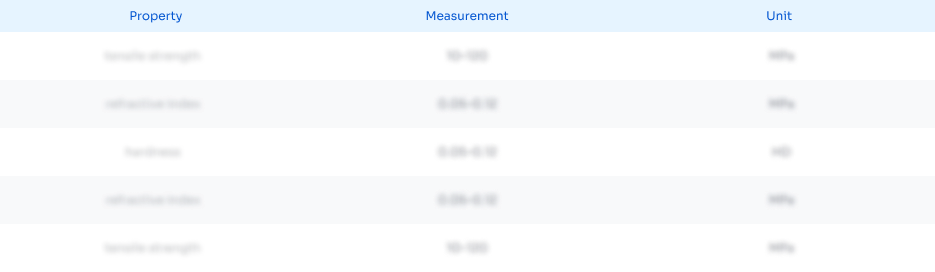
Abstract
Description
Claims
Application Information

- R&D
- Intellectual Property
- Life Sciences
- Materials
- Tech Scout
- Unparalleled Data Quality
- Higher Quality Content
- 60% Fewer Hallucinations
Browse by: Latest US Patents, China's latest patents, Technical Efficacy Thesaurus, Application Domain, Technology Topic, Popular Technical Reports.
© 2025 PatSnap. All rights reserved.Legal|Privacy policy|Modern Slavery Act Transparency Statement|Sitemap|About US| Contact US: help@patsnap.com