Pressure control structure for injection molding
A technology of pressure control and screw, which is applied in the field of pressure control structure for injection molding, can solve the problems that are difficult to realize, and can not be controlled by increasing the pressure of screw molten plastic, so as to achieve the effect of increasing production efficiency
- Summary
- Abstract
- Description
- Claims
- Application Information
AI Technical Summary
Problems solved by technology
Method used
Image
Examples
Embodiment Construction
[0023] The technical solutions in the embodiments of the present invention will be clearly and completely described below. The embodiments of the present invention and all other embodiments obtained by persons of ordinary skill in the art without making creative efforts belong to the protection scope of the present invention.
[0024] see figure see Figure 1 to Figure 5 , the present invention provides a technical solution: a pressure control structure for injection molding, including a screw 3, the screw 3 is installed in the barrel 2, the screw 3 is connected with a rotating shaft 9, and the rotating shaft 9 is installed on the first support column 8 On the top, the first support column 8 is vertically welded on the base plate 1, the rotating shaft 9 is equipped with a turntable 7, one side of the turntable 7 is provided with a speed change wheel 21, and the inside of the speed change wheel 21 is provided with a support device, the support device is formed by the first bear...
PUM
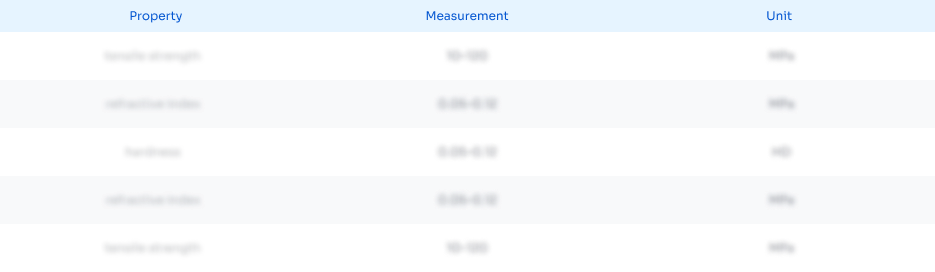
Abstract
Description
Claims
Application Information

- R&D
- Intellectual Property
- Life Sciences
- Materials
- Tech Scout
- Unparalleled Data Quality
- Higher Quality Content
- 60% Fewer Hallucinations
Browse by: Latest US Patents, China's latest patents, Technical Efficacy Thesaurus, Application Domain, Technology Topic, Popular Technical Reports.
© 2025 PatSnap. All rights reserved.Legal|Privacy policy|Modern Slavery Act Transparency Statement|Sitemap|About US| Contact US: help@patsnap.com