Optical position encoder
A technology of optical encoders and lasers, applied in the field of optical encoders, can solve problems such as large form factors and bill of materials, increase manufacturing costs, and electrical signal errors, and achieve low form factor, low system cost, and low cost effects
- Summary
- Abstract
- Description
- Claims
- Application Information
AI Technical Summary
Problems solved by technology
Method used
Image
Examples
Embodiment Construction
[0056] In general, the present disclosure provides a low-cost optical encoder solution that relies on measured reflections from a moving target to determine the position of the target.
[0057] Some examples of solutions are given in the accompanying drawings.
[0058] figure 2 An optical encoder device 200 according to the present disclosure is shown. The optical encoder device 200 includes a transmitter 202 and a sensor module 204 in the form of an IR VCSEL. The sensor module 204 includes a sensor 206 in the form of an IR SPAD, signal conditioning circuitry (not shown), and a processor 208 .
[0059] In use, the emitter 202 is configured to be disposed on a first side of the target to illuminate the target, and the sensor 206 is also configured to be disposed on the first side of the target to sense reflections from the target, wherein the sensed reflection depends on The location of the target within the system.
[0060] In other embodiments, the signal conditioning cir...
PUM
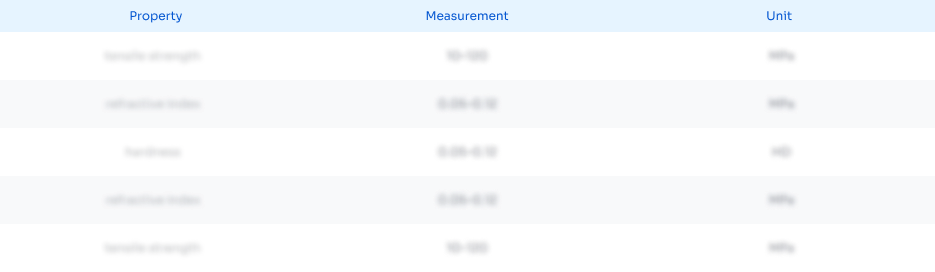
Abstract
Description
Claims
Application Information

- R&D
- Intellectual Property
- Life Sciences
- Materials
- Tech Scout
- Unparalleled Data Quality
- Higher Quality Content
- 60% Fewer Hallucinations
Browse by: Latest US Patents, China's latest patents, Technical Efficacy Thesaurus, Application Domain, Technology Topic, Popular Technical Reports.
© 2025 PatSnap. All rights reserved.Legal|Privacy policy|Modern Slavery Act Transparency Statement|Sitemap|About US| Contact US: help@patsnap.com