Three-dimensional scanning distance measuring device and method
A technology of three-dimensional scanning and ranging devices, which is applied in the direction of measuring devices, optical devices, instruments, etc., can solve problems such as complex structures of three-dimensional laser scanners, improve frame rate and point cloud density, improve frame rate and pixel resolution The effect of improving the accuracy of distance measurement
- Summary
- Abstract
- Description
- Claims
- Application Information
AI Technical Summary
Problems solved by technology
Method used
Image
Examples
Embodiment 1
[0031] An embodiment of the present invention provides a three-dimensional scanning ranging device, such as figure 1 As shown, the device includes: an optical scanning chip 1, a focusing lens 2, a light receiving element 3 and a microprocessor, and the optical scanning chip 1 is used to sequentially scan and output a line spot of multiple angles onto the object to be measured; the focusing lens 2 is used to sequentially focus multiple light beams reflected by the object to be measured under the irradiation of multiple one-line light spots; the light receiving element 3 is used to sequentially receive multiple light beams focused by the focusing lens 2 to obtain multiple images containing bright spots image; the microprocessor is connected to the light-receiving element 3, and is used to receive multiple images containing bright spots. The image of the spot is analyzed to obtain the three-dimensional point cloud of the object to be measured. Among them, images containing light...
Embodiment 2
[0039] An embodiment of the present invention provides a three-dimensional scanning ranging method, such as image 3 As shown, the method includes the following steps:
[0040] Step S101: Sequentially scan and output one-line spots of multiple scanning angles to irradiate the object to be tested; in one embodiment, an optical scanning chip can be used to scan back and forth vertical one-line spots in the horizontal direction, wherein the light scanning The chip can choose any one of optical phased array, optical switch, and MEMS optical scanning mirror.
[0041] Step S102: Receive multiple light beams reflected by the object to be measured under the irradiation of multiple inline light spots and focus them sequentially; specifically, a focusing lens can be used to receive multiple light beams reflected by the object to be measured under the irradiation of multiple inline light spots For focusing, other elements may also be used to achieve focusing of the light beam, which is ...
Embodiment 3
[0052] An embodiment of the present invention provides a three-dimensional scanning ranging method, which is divided into two processes of calibration and measurement. Wherein, the first relationship between the position of the light spot and the depth of the object is firstly determined through calibration, and then the depth of the object to be measured is measured by using the first relationship.
[0053] In one embodiment, y=f(a0,a1,...an,x) is used to describe the nonlinear relationship between the bright spot position x and the object depth y, and there are n constants to be determined in this relationship, and these n Constants can be obtained by distance calibration. That is, by actually measuring n y-values and x-values, an equation system of n equations is formed to solve the values of a0~an. Since too many constants will increase the complexity of the calibration, n=3 can be selected. In a specific implementation, the relationship between x and y can be descri...
PUM
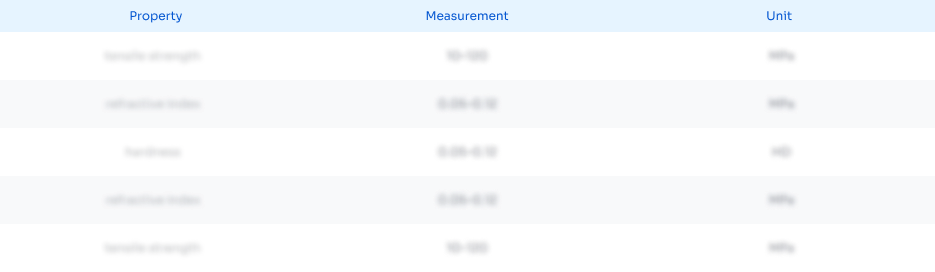
Abstract
Description
Claims
Application Information

- R&D Engineer
- R&D Manager
- IP Professional
- Industry Leading Data Capabilities
- Powerful AI technology
- Patent DNA Extraction
Browse by: Latest US Patents, China's latest patents, Technical Efficacy Thesaurus, Application Domain, Technology Topic.
© 2024 PatSnap. All rights reserved.Legal|Privacy policy|Modern Slavery Act Transparency Statement|Sitemap