Application method based on EOASM algorithm in construction of agent model of stacking robot driving arm base
A palletizing robot and proxy model technology, which is applied in the field of proxy model construction of the driving arm base of the palletizing robot, can solve the problems of increasing the failure rate of parts, consuming manpower and material resources, fatigue damage, etc., and achieves wide application prospects and convenient and concise processes. Effect
- Summary
- Abstract
- Description
- Claims
- Application Information
AI Technical Summary
Problems solved by technology
Method used
Image
Examples
Embodiment Construction
[0031] In order to make the object, technical solution and advantages of the present invention clearer, the present invention will be further described in detail below in conjunction with the accompanying drawings and embodiments. It should be understood that the specific embodiments described here are only used to explain the present invention, not to limit the present invention.
[0032] Such as figure 1 As shown, it is a schematic flowchart of an application method of the present invention based on the EOASM algorithm in the construction of the agent model of the driving arm base of the palletizing robot. An application method of a combined proxy model construction method based on local error expectation plus points in the construction of a proxy model for a palletizing robot driven arm base, including the following steps:
[0033] A. Establish the geometric model of the palletizing robot drive arm seat;
[0034] B. Carry out material configuration for the geometric model...
PUM
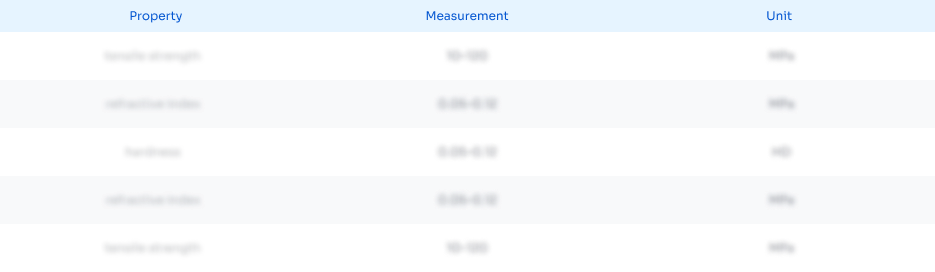
Abstract
Description
Claims
Application Information

- R&D Engineer
- R&D Manager
- IP Professional
- Industry Leading Data Capabilities
- Powerful AI technology
- Patent DNA Extraction
Browse by: Latest US Patents, China's latest patents, Technical Efficacy Thesaurus, Application Domain, Technology Topic, Popular Technical Reports.
© 2024 PatSnap. All rights reserved.Legal|Privacy policy|Modern Slavery Act Transparency Statement|Sitemap|About US| Contact US: help@patsnap.com