Welding method capable of reducing inclusion defects in medium-thickness plate weld joints
A welding method and defect technology, applied in the field of welding that can reduce inclusion defects inside welds of medium and thick plates, can solve the problems of restricting the service life of the hull, increasing the labor intensity of workers, and affecting the quality of the hull, so as to improve the quality of welding Quality and welding efficiency, improving welding quality, and avoiding the effect of mechanical property decline
- Summary
- Abstract
- Description
- Claims
- Application Information
AI Technical Summary
Problems solved by technology
Method used
Image
Examples
Embodiment 1
[0035] For V-groove
[0036] The welding method comprises: at first carrying out the first welding and cleaning: performing continuous laser and MIG composite welding, forming the first welding seam in the V-shaped groove, and forming the first welding seam in the welding seam (the welding seam refers to the first welding seam) The welding seam formed during the welding seam) is formed and the cleaning laser is turned on synchronously. After the cleaning laser is cleaned in time and effectively, the metal color of the first welding seam is exposed.
[0037] It should be noted that the term "starting the cleaning laser synchronously after the weld seam is formed" does not refer to turning on the cleaning laser after the first weld seam is completely formed, but refers to Turn on the cleaning laser as soon as the initial weld seam is formed. These terms have the same meaning hereinafter.
[0038] Then, repeat the first welding and cleaning, so that the first welding seam gradu...
Embodiment 2
[0048] For Y-groove
[0049] The welding method includes: firstly perform the first welding and cleaning: turn on the continuous laser to form the first weld in the Y-shaped groove, and turn on the cleaning laser synchronously after the weld is formed to clean the first Weld so that the first weld reveals the metallic color.
[0050] Then carry out the second welding and cleaning: carry out continuous laser and MIG hybrid welding, form the second welding seam on the surface of the first welding seam, and turn on the cleaning laser synchronously after the welding seam is formed, so that the The second weld reveals the metallic color.
[0051] Finally, repeat the second welding and cleaning until the Y-shaped openings at the welds to be welded are filled.
[0052] The size of the blunt edge is designed according to the maximum depth-to-width ratio of the weld that does not allow welding defects. Generally, the gap between the two blunt sides of the Y-shaped groove is smaller ...
PUM
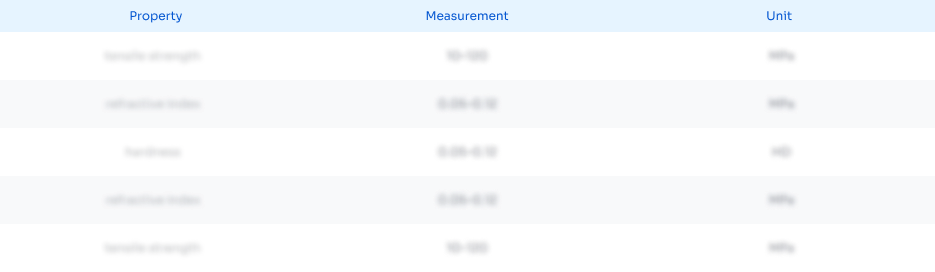
Abstract
Description
Claims
Application Information

- Generate Ideas
- Intellectual Property
- Life Sciences
- Materials
- Tech Scout
- Unparalleled Data Quality
- Higher Quality Content
- 60% Fewer Hallucinations
Browse by: Latest US Patents, China's latest patents, Technical Efficacy Thesaurus, Application Domain, Technology Topic, Popular Technical Reports.
© 2025 PatSnap. All rights reserved.Legal|Privacy policy|Modern Slavery Act Transparency Statement|Sitemap|About US| Contact US: help@patsnap.com