Inner wall structure of hazardous waste incineration rotary kiln
A rotary kiln and hazardous waste technology, applied in the direction of incinerator, combustion type, combustion method, etc., can solve the problems of poor stirring effect, affecting incineration effect, uneven heating of hazardous waste, etc., to achieve good effect, strong wear resistance, and improved the effect of burning
- Summary
- Abstract
- Description
- Claims
- Application Information
AI Technical Summary
Problems solved by technology
Method used
Image
Examples
Embodiment 1
[0033] The structure of the inner wall of the rotary kiln for hazardous waste incineration is basically as attached figure 1 As shown, it includes multiple sets of material dispersion structures arranged in sequence from left to right, combined with figure 2 As shown, the material dispersion structure includes a plurality of refractory bumps 1 arranged circumferentially along the inner wall of the cylinder 3 of the rotary kiln. The number of refractory bumps 1 is set according to actual needs. In this embodiment, there are 22 refractory bumps 1 ; The refractory bumps 1 of the material dispersion structure are connected end to end, and the refractory bumps 1 use refractory bricks.
[0034] The refractory bumps 1 of the material dispersing structure are all arranged in a dislocation in height, and each group of material dispersing structures are arranged in a dislocation in height. In this embodiment, the dislocation arrangement of the refractory bump 1 of the material dispers...
Embodiment 2
[0041] The difference between embodiment 2 and embodiment 1 is that in this embodiment, the dislocation arrangement of the refractory bumps 1 of the material dispersion structure is that the material dispersion structure includes multiple sets of refractory bump groups, and the refractory bump groups include A high refractory bump and a low refractory bump, the thickness difference between two adjacent refractory bumps 1 is 100mm, and the thickness of the two adjacent refractory bumps 1 with a larger thickness is the same, that is, the dispersed structure of each group of materials The thickness of the refractory bump 1 is set according to the cycle of a, a+100mm, a...a, a+100mm.
[0042]The dislocation method of the material dispersion structure is that the thickness difference between two adjacent groups of material dispersion structures is 100 mm, that is, the thickness difference between two adjacent refractory bumps 1 of the adjacent two groups of material dispersion struc...
Embodiment 3
[0045] Embodiment 3 differs from Embodiment 1 only in that, as image 3 As shown, in this embodiment, each group of material dispersion structure is provided with 32 pieces of refractory bumps 1, and the dislocation arrangement of the refractory bumps 1 of the material dispersion structure is that the 4 pieces of refractory bumps adjacent to each group of material dispersion structure The block 1 is marked as A, and the refractory bump 1 adjacent to A is marked as B, and the thickness of B is 50mm larger than that of A, that is, the refractory bump 1 of each group of material dispersion structure is in accordance with A, B, A. ..... Cycle settings for A and B.
[0046] The dislocation setting method of the material dispersion structure is as follows: Figure 4 As shown, the adjacent four groups of material dispersion structures are marked as X, and the group of material dispersion structures adjacent to X is marked as Y. The thickness of Y is 50mm larger than the thickness of...
PUM
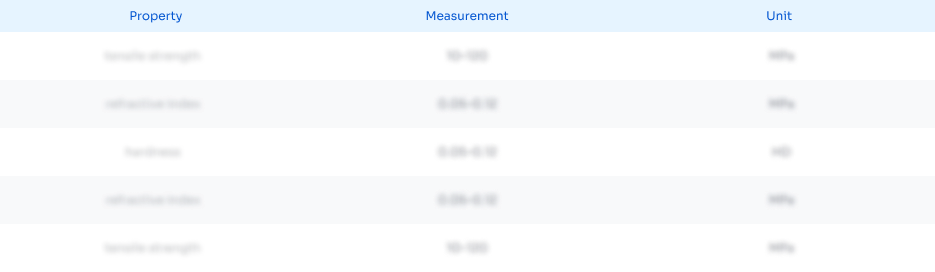
Abstract
Description
Claims
Application Information

- Generate Ideas
- Intellectual Property
- Life Sciences
- Materials
- Tech Scout
- Unparalleled Data Quality
- Higher Quality Content
- 60% Fewer Hallucinations
Browse by: Latest US Patents, China's latest patents, Technical Efficacy Thesaurus, Application Domain, Technology Topic, Popular Technical Reports.
© 2025 PatSnap. All rights reserved.Legal|Privacy policy|Modern Slavery Act Transparency Statement|Sitemap|About US| Contact US: help@patsnap.com