Forging and normalizing process for synchronizer tooth holder with double-sided oil grooves
A technology of synchronizer and oil groove, which is applied in the field of forging and normalizing technology of the gear seat of the synchronizer with double-sided oil groove, which can solve the problems of subsequent fine turning and high-speed gear shaping that cannot be carried out normally, and large hardness dispersion, so as to reduce Effects of labor cost, improved cooling and lubrication, and increased productivity
- Summary
- Abstract
- Description
- Claims
- Application Information
AI Technical Summary
Problems solved by technology
Method used
Image
Examples
Embodiment Construction
[0022] The technical solution of the present invention will be clearly and completely described below in conjunction with the accompanying drawings, but this embodiment should not be construed as limiting the present invention.
[0023] The present invention as figure 1 Shown:
[0024] A forging and normalizing process for a tooth seat of a synchronizer with double-sided oil grooves,
[0025] (1) In order to realize the forging of the gear seat of the synchronizer with double-sided oil grooves, a forging die is adopted. The structure of the forging die is: including an upper die plate 1 and a lower die plate 2, wherein:
[0026] The upper part of the upper template 1 is fixed with a moving spindle 3 of the forging press, and a mold cavity is arranged on the lower end surface of the upper template 1. In the middle of the mold cavity, a perforating punch 4 extending downward is fixed. The outer peripheral surface of the perforating punch is from inside to outside. The forming ...
PUM
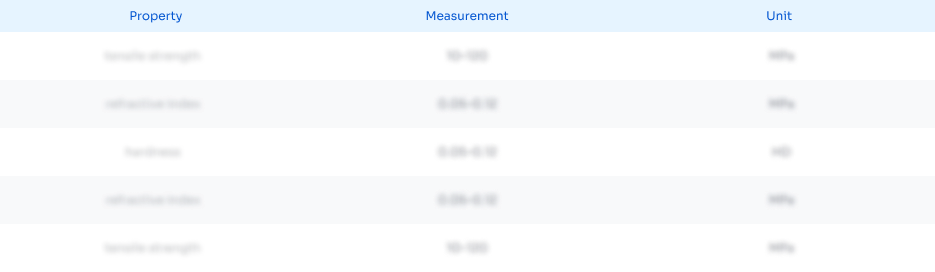
Abstract
Description
Claims
Application Information

- R&D
- Intellectual Property
- Life Sciences
- Materials
- Tech Scout
- Unparalleled Data Quality
- Higher Quality Content
- 60% Fewer Hallucinations
Browse by: Latest US Patents, China's latest patents, Technical Efficacy Thesaurus, Application Domain, Technology Topic, Popular Technical Reports.
© 2025 PatSnap. All rights reserved.Legal|Privacy policy|Modern Slavery Act Transparency Statement|Sitemap|About US| Contact US: help@patsnap.com