Hydrophone sensitivity calibration method based on sine function fitting
A calibration method and sine function technology, applied to vibration measurement in instruments and fluids, measuring vibration and other directions, can solve the problems of poor repeatability, low sensitivity and accuracy, and achieve the effect of avoiding influence, improving accuracy and eliminating accidental errors.
- Summary
- Abstract
- Description
- Claims
- Application Information
AI Technical Summary
Problems solved by technology
Method used
Image
Examples
Embodiment
[0043] This embodiment is verified by simulation experiments. The initial conditions of the experiment are as follows: the sound source frequency is 500 Hz, the sensitivity of the standard hydrophone is -200 dB, the peak-to-peak output of the standard hydrophone is 0.5 V, and the peak-to-peak output of the hydrophone to be tested is 50 μV. The sensitivity of the standard hydrophone is theoretically -120dB. The sampling frequency of the two hydrophones needs to satisfy the sampling theorem, not generally. In the simulation, the sampling frequency of the hydrophone to be tested and the standard hydrophone are set to be the same, both of which are 10kHz.
[0044] Under ideal conditions, the output signals of the hydrophone to be tested and the standard hydrophone are single-frequency sinusoidal signals with the same frequency as the fundamental frequency of the sound source, respectively as figure 2 and image 3 As shown, the peak-to-peak output signals of the hydrophone under ...
PUM
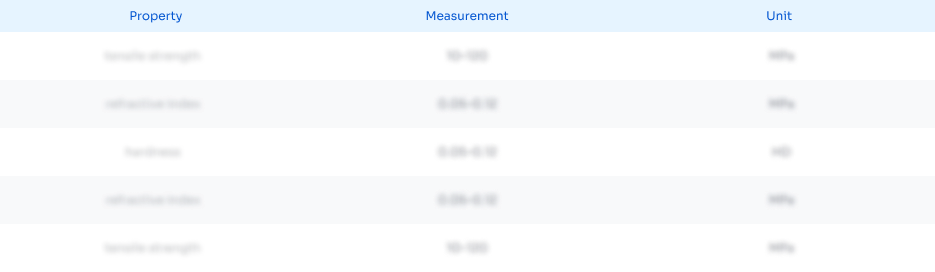
Abstract
Description
Claims
Application Information

- R&D
- Intellectual Property
- Life Sciences
- Materials
- Tech Scout
- Unparalleled Data Quality
- Higher Quality Content
- 60% Fewer Hallucinations
Browse by: Latest US Patents, China's latest patents, Technical Efficacy Thesaurus, Application Domain, Technology Topic, Popular Technical Reports.
© 2025 PatSnap. All rights reserved.Legal|Privacy policy|Modern Slavery Act Transparency Statement|Sitemap|About US| Contact US: help@patsnap.com