Active control airfoil device and system of maglev train
A maglev train and active control technology, applied in the fields of noise, maglev train dynamics, and active control, can solve problems such as poor economic performance indicators, and achieve the effect of reducing energy consumption and improving braking capacity
- Summary
- Abstract
- Description
- Claims
- Application Information
AI Technical Summary
Problems solved by technology
Method used
Image
Examples
Embodiment 1
[0032] An active control airfoil device for a maglev train, such as Figure 1~3 As shown, it is arranged on the top of the maglev train 1, including the main airfoil 2 and the flap 3 connected to the rear edge of the main airfoil 2, the main airfoil 2 is located above the top of the maglev train 1, and can be relative to the maglev train 1 through the reversing assembly 4 The top rotates, and the angle between the flap 3 and the main airfoil 2 can be adjusted through the servo assembly 5 .
[0033] In this embodiment, the reversing assembly 5 in the present invention can use the electric energy of the maglev train 1, and is responsible for horizontally turning the direction of the main airfoil 2 during the stop and reversing of the maglev train 1, so that it faces the running direction of the maglev train 1. The steering assembly 5 maintains a locked state during the operation of the maglev train 1 . The main airfoil 2 is arranged on the reversing assembly 4 through the brack...
Embodiment 2
[0037] An active control airfoil system for a maglev train, comprising the active control airfoil device of Embodiment 1. Preferably the actively controlled airfoil system further comprises a controller. The controller is used to obtain train operation instructions and operation speed signals from the maglev train, convert the train operation instructions and operation speed signals to the servo components, and control the rotation angle of the flaps. At the same time, the controller also outputs to the maglev control system of the maglev train. Feedback, the maglev train system uses this to adjust the magnetic buoyancy. Further preferably, the controller is also used to convert the train operation command signal and transmit it to the reversing assembly, so that the maglev train controls the main airfoil to face the train running direction before the reversing operation. The controller can be independent of the maglev train control system (for example, using an independent s...
PUM
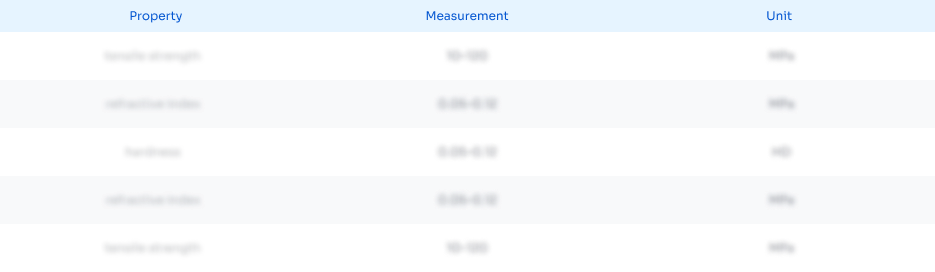
Abstract
Description
Claims
Application Information

- R&D Engineer
- R&D Manager
- IP Professional
- Industry Leading Data Capabilities
- Powerful AI technology
- Patent DNA Extraction
Browse by: Latest US Patents, China's latest patents, Technical Efficacy Thesaurus, Application Domain, Technology Topic, Popular Technical Reports.
© 2024 PatSnap. All rights reserved.Legal|Privacy policy|Modern Slavery Act Transparency Statement|Sitemap|About US| Contact US: help@patsnap.com