Valve flow coefficient convenient calculation method based on CFD simulation
A calculation method and simulation calculation technology, applied in the direction of calculation, computer-aided design, design optimization/simulation, etc., can solve the problems of high valve flow coefficient cost, valve size specification limit, large calculation result error, etc., to shorten the research and development cycle, The effect of avoiding waste and saving costs
- Summary
- Abstract
- Description
- Claims
- Application Information
AI Technical Summary
Problems solved by technology
Method used
Image
Examples
Embodiment Construction
[0037] The operation process of this embodiment is as follows:
[0038] (1) Based on the 3D model of the valve assembly, extract the flow field models of the upstream pipeline, the valve, and the downstream pipeline; taking the DN500 central butterfly valve as an example, use Solidworks to establish the assembly model such as figure 2 , after simplifying the small structures such as rounding, chamfering and threaded holes in this model, the inlet and outlet are respectively connected with an upstream pipeline with a length of 21 times the nominal diameter and a downstream pipeline with a length of 10 times the nominal diameter; then extract the upstream pipeline, valve, The "valve-pipe" flow field model of the combination of downstream pipelines, such as image 3 , to symmetrically divide the flow field model to save computing resources;
[0039] (2) Mesh the flow field model, consider the flow boundary conditions required by the working conditions, and combine multiple mesh...
PUM
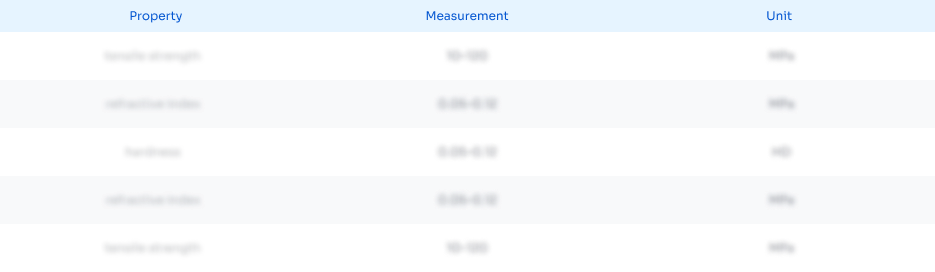
Abstract
Description
Claims
Application Information

- R&D
- Intellectual Property
- Life Sciences
- Materials
- Tech Scout
- Unparalleled Data Quality
- Higher Quality Content
- 60% Fewer Hallucinations
Browse by: Latest US Patents, China's latest patents, Technical Efficacy Thesaurus, Application Domain, Technology Topic, Popular Technical Reports.
© 2025 PatSnap. All rights reserved.Legal|Privacy policy|Modern Slavery Act Transparency Statement|Sitemap|About US| Contact US: help@patsnap.com