Joint production line for spun-laced nonwoven fabric
A non-woven fabric and production line technology, applied in textile and paper making, drying gas arrangement, fabric surface trimming, etc., can solve the problems of increasing the workload of staff, occupying more space, reducing work efficiency, etc., to reduce temperature and convenience. Operation and use, the effect of improving work efficiency
- Summary
- Abstract
- Description
- Claims
- Application Information
AI Technical Summary
Problems solved by technology
Method used
Image
Examples
Embodiment 1
[0035] see Figure 1-8 , according to an embodiment of the present invention, a combined production line of spunlace nonwoven fabrics includes a base plate 1, a box body 2 is fixed at one end of the base plate 1, and a drying device is provided inside the box body 2, Both sides of the box body 2 are provided with an inlet and outlet, and one side of the box body 2 is provided with an air cooling device, and the wind cooling device is equipped with a winding device on one side of the box body 2. A pressing device is provided above the winding device, and the drying device includes a fan 3, one end of the fan 3 is provided with an air inlet hood 4, and the end of the fan 3 far away from the air inlet hood 4 is provided with a connecting pipe 5. The end of the communication pipe 5 far away from the fan 3 is in communication with the heating box 6, and a number of heating nets 7 are arranged inside the heating box 6, and the end of the heating box 6 far away from the communication...
Embodiment 2
[0037] see Figure 1-8 , for the air-cooled device, the air-cooled device includes a second motor 44, the output end of the second motor 44 is provided with a rotating shaft, and the end of the rotating shaft away from the second motor 44 is fixedly provided with a fan 45, The air-cooling device can air-cool and dissipate heat on the surface of the nonwoven fabric after heating and drying, thereby reducing the temperature of the surface of the nonwoven fabric, thereby facilitating winding and collection; for the second motor 44, the second motor 44 Located in the inside of the placement frame 46, the other side of the placement frame 46 is fixedly connected to the side wall of the box body 2, the placement frame 46 can support the second motor 44, avoiding the second motor 24 Placed in the air, thereby increasing the safety of the second motor 44 in use.
Embodiment 3
[0039] see figure 1 , for the guide roller set, the guide roller set includes several guide rollers 47, the two sides of the guide rollers 47 are connected to the top of the box body 2 through the hanger 48, and the guide rollers 47 are located at different heights. on the horizontal plane, and it is connected with the inner wall of the box body 2 by hangers 48 of different lengths, so as to realize the support for the guide roller 47, the nonwoven fabric passes through the guide rollers in turn, and the two sides of the box body 2 are provided with Import and export, so as to realize the entry of non-woven fabrics, and then pass through the box body 2 to connect with the winding shaft 14. By passing the non-woven fabrics through the guide roller group, the time of the non-woven fabrics in the box body 2 can be increased, thereby improving Drying efficiency of nonwovens.
PUM
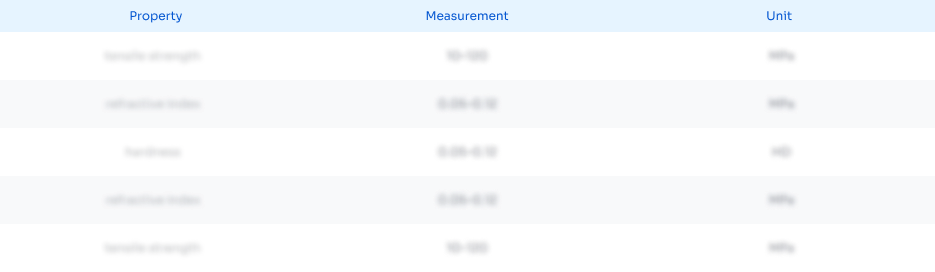
Abstract
Description
Claims
Application Information

- R&D
- Intellectual Property
- Life Sciences
- Materials
- Tech Scout
- Unparalleled Data Quality
- Higher Quality Content
- 60% Fewer Hallucinations
Browse by: Latest US Patents, China's latest patents, Technical Efficacy Thesaurus, Application Domain, Technology Topic, Popular Technical Reports.
© 2025 PatSnap. All rights reserved.Legal|Privacy policy|Modern Slavery Act Transparency Statement|Sitemap|About US| Contact US: help@patsnap.com