Optimization method of vehicle drag coefficient based on adaptive surrogate model
An adaptive proxy and drag coefficient technology, which is applied in design optimization/simulation, special data processing applications, geometric CAD, etc., can solve problems such as low optimization efficiency, complicated operation, and long time consumption, and meet the requirements of reducing R&D costs and engineering experience Low, the effect of reducing the number of calls
- Summary
- Abstract
- Description
- Claims
- Application Information
AI Technical Summary
Problems solved by technology
Method used
Image
Examples
Embodiment Construction
[0033] It should be noted that, in the case of no conflict, the embodiments of the present invention and the features in the embodiments can be combined with each other.
[0034] The present invention will be described in detail below with reference to the accompanying drawings and examples.
[0035] Such as figure 1 As shown, the vehicle drag coefficient optimization method based on the adaptive proxy model includes the following steps:
[0036] A. Carry out CFD simulation calculation on the initial model of the car to obtain the calculated value of the drag coefficient of the initial model;
[0037] B. Select the design variables and determine the variation range of the design variables;
[0038] C. Construct a parametric model based on the initial model;
[0039] D. Select a sample point and store it in the sample point database;
[0040] E. Calculate the drag coefficient calculation value corresponding to the sample point based on the parameterized model, and store it ...
PUM
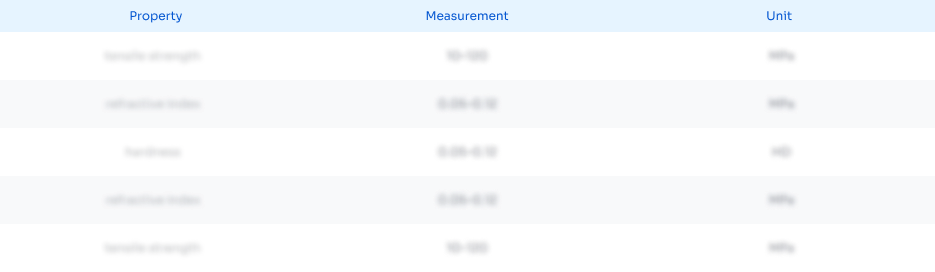
Abstract
Description
Claims
Application Information

- Generate Ideas
- Intellectual Property
- Life Sciences
- Materials
- Tech Scout
- Unparalleled Data Quality
- Higher Quality Content
- 60% Fewer Hallucinations
Browse by: Latest US Patents, China's latest patents, Technical Efficacy Thesaurus, Application Domain, Technology Topic, Popular Technical Reports.
© 2025 PatSnap. All rights reserved.Legal|Privacy policy|Modern Slavery Act Transparency Statement|Sitemap|About US| Contact US: help@patsnap.com