A differential heavy-duty fine-tuning mechanism
A technology of fine-tuning mechanism and moving column, applied in instrument, installation, optics and other directions, can solve the problem of inability to meet the needs of use, and achieve the effect of shortening the development cycle, compact structure, and easy assembly.
- Summary
- Abstract
- Description
- Claims
- Application Information
AI Technical Summary
Problems solved by technology
Method used
Image
Examples
Embodiment Construction
[0028] In order to enable those skilled in the art to better understand the technical solutions of the present invention, the present invention will be further described in detail below in conjunction with the accompanying drawings.
[0029] see figure 1 shown;
[0030] Invented a differential heavy-duty fine-tuning mechanism, including:
[0031] Adjustment stud 1;
[0032] One end of the nut shell 2 is threadedly connected to the adjusting stud 1, and the side wall of the nut shell 2 away from the end of the adjusting stud 1 is provided with a guide groove along the axial direction;
[0033] The micro-movement column 3 is slidably connected to the end of the nut shell 2 away from the adjustment screw 1, and the side wall of the micro-motion column 3 is fixedly connected with a guide pin 4, which is used to limit the micro-motion column 3 around the axis of the nut shell 2 in a sliding connection with the guide groove Rotational degrees of freedom;
[0034] The micro-movem...
PUM
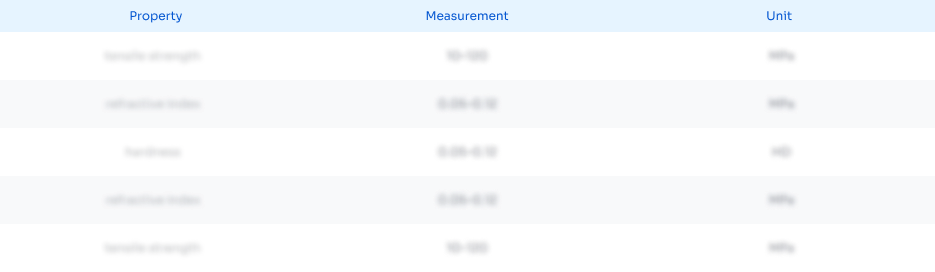
Abstract
Description
Claims
Application Information

- R&D Engineer
- R&D Manager
- IP Professional
- Industry Leading Data Capabilities
- Powerful AI technology
- Patent DNA Extraction
Browse by: Latest US Patents, China's latest patents, Technical Efficacy Thesaurus, Application Domain, Technology Topic, Popular Technical Reports.
© 2024 PatSnap. All rights reserved.Legal|Privacy policy|Modern Slavery Act Transparency Statement|Sitemap|About US| Contact US: help@patsnap.com