Automatic layering placement rack for workpieces
An automatic layering and workpiece technology, applied in the directions of internal accessories, external accessories, bottle/can components, etc., can solve the problems of a small number of support blocks, a small number of workpieces, and the failure of the material rack to achieve linkage, so as to protect the workpiece, Simple structure and the effect of preventing collision damage
- Summary
- Abstract
- Description
- Claims
- Application Information
AI Technical Summary
Problems solved by technology
Method used
Image
Examples
Embodiment 1
[0069] In this embodiment, a workpiece is automatically layered and placed on the material rack. The workpiece to be positioned is described by taking the lower cover of the new energy battery as an example, as shown in Figure 1 to Figure 13 As shown, the pedestal 10 comprising a frame-like structure is composed of a rectangular base 11 and a plurality of pedestals 12 such as 6 perpendicular to the upper surface of the pedestal 11, and the 6 pedestals 12 are divided into two parts. There are three groups in total, one group is arranged on a pair of short sides of the base 11, and the other two groups are arranged at intervals on a group of long sides of the base 11; each base column 12 is provided with an installation cavity 121, the installation cavity 121 is rotated with a linkage positioning mechanism 20; the three sets of linkage positioning components in the three groups of base columns 12 jointly define a positioning space (not shown) for positioning and supporting the w...
PUM
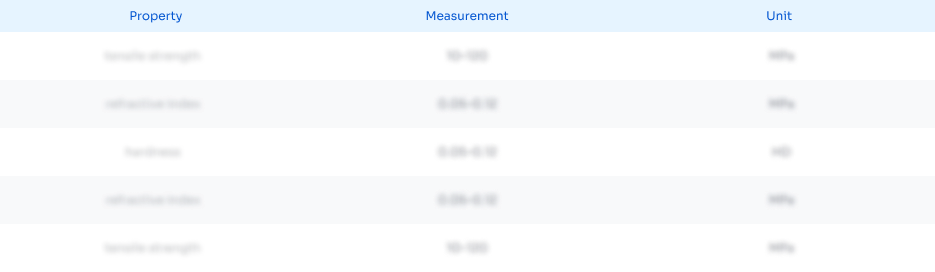
Abstract
Description
Claims
Application Information

- Generate Ideas
- Intellectual Property
- Life Sciences
- Materials
- Tech Scout
- Unparalleled Data Quality
- Higher Quality Content
- 60% Fewer Hallucinations
Browse by: Latest US Patents, China's latest patents, Technical Efficacy Thesaurus, Application Domain, Technology Topic, Popular Technical Reports.
© 2025 PatSnap. All rights reserved.Legal|Privacy policy|Modern Slavery Act Transparency Statement|Sitemap|About US| Contact US: help@patsnap.com