Thin plate rear end automatic loading system for electronic saw
A technology of automatic feeding and power system, applied in the field of sheet metal processing, can solve the problems of low power; rear feeding electronic saw, rear feeding, affecting the quality of thin plate sawing, and high physical energy consumption of operators.
- Summary
- Abstract
- Description
- Claims
- Application Information
AI Technical Summary
Problems solved by technology
Method used
Image
Examples
Embodiment 1
[0020] Embodiment 1: An automatic feeding system for the rear end of an electronic saw thin plate, including a frame 1, an auxiliary feeding unit 2, a main feeding unit 3, a power system and an intelligent control system; a transmission plate 11 is fixed on the frame, and the frame 1 A pair of longitudinal beams 12 are fixed on both sides, the main feeding unit 3 is fixed on the frame 1 through the longitudinal beams 12; the auxiliary feeding unit 2 is located at the front end of the frame 1, and the power system is controlled by an intelligent control system to realize The plate is pushed onto the transfer plate 11 by the auxiliary feeding unit 2, and then sent out by the main feeding unit 3.
[0021] Described frame 1 comprises machine pier 13, transmission plate 11, support column 14 and longitudinal beam 12, by described machine pier 13 and support column 14, transmission plate 11 is fixed above support column 14, and longitudinal beam 12 is fixed on transmission On both s...
PUM
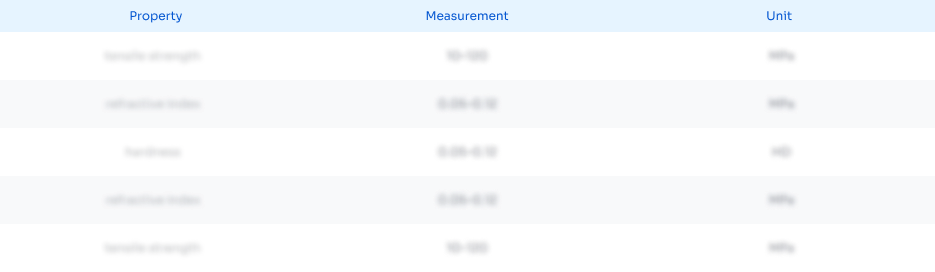
Abstract
Description
Claims
Application Information

- R&D
- Intellectual Property
- Life Sciences
- Materials
- Tech Scout
- Unparalleled Data Quality
- Higher Quality Content
- 60% Fewer Hallucinations
Browse by: Latest US Patents, China's latest patents, Technical Efficacy Thesaurus, Application Domain, Technology Topic, Popular Technical Reports.
© 2025 PatSnap. All rights reserved.Legal|Privacy policy|Modern Slavery Act Transparency Statement|Sitemap|About US| Contact US: help@patsnap.com