Production process of roller assembly
A production process and roller technology, which is applied in the field of roller component production technology, can solve the problems of low assembly efficiency, low production efficiency of rollers, time-consuming and labor-intensive problems, and achieve the effects of improving production efficiency, improving assembly efficiency, and speeding up glue spraying efficiency
- Summary
- Abstract
- Description
- Claims
- Application Information
AI Technical Summary
Problems solved by technology
Method used
Examples
Embodiment 1
[0023] A production process of a roller assembly, the assembly process includes the following steps:
[0024] A. Assembling the roller and the round tube: put a certain number of rollers on the round tube;
[0025] B. Glue spraying: use the glue spraying device to spray glue on the side of the roller;
[0026] C. Vulcanization treatment: put the roller into the oven for vulcanization;
[0027] D. Pouring polyurethane: put the roller into the mold, and pour polyurethane into the roller with a pouring machine;
[0028] E. Cutting: After the polyurethane is solidified, take the roller out of the mold, and cut the roller with a cutting device;
[0029] F. Assembly: Assemble the rollers, shafts and bearings with assembly equipment.
[0030] Compared with the existing technology, the advantage of this production process of the roller assembly is that: putting the roller on the round pipe, and then using the glue spraying device to spray glue on the roller in a concentrated manner...
Embodiment 2
[0039] In this embodiment, in the step B, the glue spraying device consists of a frame, a discharge seat, a transfer assembly, a rotary drive assembly, a glue spray assembly and a material receiving seat, the rotary drive assembly is installed on the frame, and the discharge The seat and the material receiving seat are arranged on both sides of the rotary drive assembly, the transfer assembly is slidably installed between the discharge seat and the material receiving seat, the glue spray assembly is slidably installed on the frame, and the glue spray assembly is located above the rotary drive assembly. The specific working process is: the round tube passes through the through hole in the middle of the rollers, the rollers are arranged along the round tube, each string of rollers is arranged on the discharge seat in turn, the transfer component transfers the round tube with the rollers to the rotary drive component, and then The rotating drive assembly drives the roller to rotat...
PUM
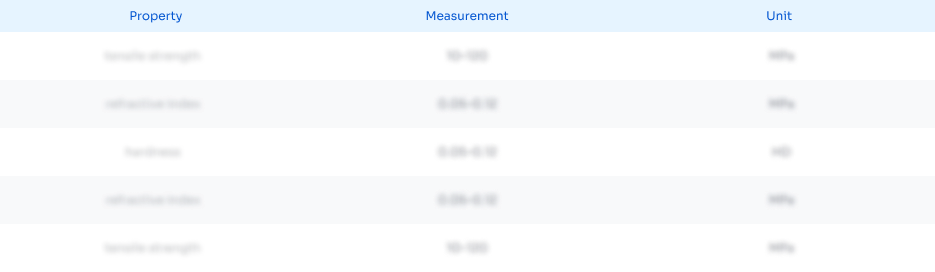
Abstract
Description
Claims
Application Information

- Generate Ideas
- Intellectual Property
- Life Sciences
- Materials
- Tech Scout
- Unparalleled Data Quality
- Higher Quality Content
- 60% Fewer Hallucinations
Browse by: Latest US Patents, China's latest patents, Technical Efficacy Thesaurus, Application Domain, Technology Topic, Popular Technical Reports.
© 2025 PatSnap. All rights reserved.Legal|Privacy policy|Modern Slavery Act Transparency Statement|Sitemap|About US| Contact US: help@patsnap.com