Grabbing operation system for mobile robot and control method
A mobile robot and operating system technology, applied in the field of autonomous grasping operations, can solve the problems of limiting the service capability and operation efficiency of intelligent mobile robots, relying on structured environment, and being difficult to replace humans to complete service work autonomously.
- Summary
- Abstract
- Description
- Claims
- Application Information
AI Technical Summary
Problems solved by technology
Method used
Image
Examples
Embodiment Construction
[0060] The technical solution of the present invention will be further described in detail below in conjunction with the accompanying drawings of the specification.
[0061] Such as Figure 1-4 As shown, the present invention provides a mobile robot grasping operation system, including the following parts:
[0062] The intelligent sensing unit 10 is composed of a basic sensing unit, a two-axis pan / tilt head 13, a processor 8 and an embedded computing platform 4. The basic sensing unit is composed of a monocular camera 11 and a single-line laser ranging module 12. The laser ranging module 12 is driven by a small two-axis pan / tilt 13; the processor 8 uses a single-chip microcomputer to process the information of the laser ranging module 12, the control of the pan / tilt motor and the calculation of the three-dimensional coordinates of the object; the embedded computing platform 4 is respectively connected with the monocular camera 11, The processor 8 is connected to process the object...
PUM
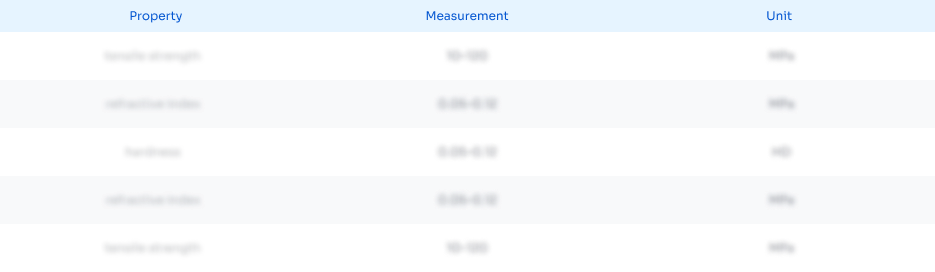
Abstract
Description
Claims
Application Information

- R&D
- Intellectual Property
- Life Sciences
- Materials
- Tech Scout
- Unparalleled Data Quality
- Higher Quality Content
- 60% Fewer Hallucinations
Browse by: Latest US Patents, China's latest patents, Technical Efficacy Thesaurus, Application Domain, Technology Topic, Popular Technical Reports.
© 2025 PatSnap. All rights reserved.Legal|Privacy policy|Modern Slavery Act Transparency Statement|Sitemap|About US| Contact US: help@patsnap.com