Shuttle machine speed changing mechanism
A speed change mechanism and shuttle machine technology, which is applied in the direction of mechanical equipment, gear transmission devices, and components with teeth, etc., can solve the problems of excessive volume and weight, achieve reduced occupied volume and weight, improve operational safety performance, and reduce occupancy volume effect
- Summary
- Abstract
- Description
- Claims
- Application Information
AI Technical Summary
Problems solved by technology
Method used
Image
Examples
Embodiment 1
[0032] See figure 1 with figure 2 As shown, the shuttle speed change mechanism of the present invention is schematically shown, which includes a shift lever 1, a first gear 2 and a second gear 3, wherein the number of teeth of the first gear 2 and the second gear 3 are different and It is sleeved on the shift rod 1, and the outer circumference of the shift rod 1 is axially provided with a tooth set 4, and the tooth set 4 is located between the first gear 2 and the second gear 3. What is important is that the The inside of the first gear 2 is provided with a first tooth groove 21, the inside of the second gear 3 is provided with a second tooth groove 31, and the first tooth groove 21 is used to communicate with the first end of the tooth set 4 ( figure 1 The left end of the middle tooth group 4) is mated and plugged in, and the second tooth groove 31 is used to connect with the second end of the tooth group 4 ( figure 1 The right end of the middle tooth group 4) is mated and...
Embodiment 2
[0039] See Figure 5 As shown, the difference between the shift lever 1 in this embodiment and the first embodiment is that the tooth surfaces of the first helical teeth 41 and the second helical teeth 42 are arc-shaped, which is beneficial to the first helical teeth 41 and the second helical teeth. The helical teeth 42 enter the corresponding tooth slots more smoothly, avoiding the jamming phenomenon of gear shifting, and even the tip of the helical teeth and the tooth slots are pushed against each other when shifting gears, which affects the life of the helical teeth and the tooth slots. In this way, the tooth surfaces of the helical teeth are arranged in an arc shape, which can further improve the smoothness of shifting.
[0040] Preferably, in this embodiment, see Figure 4 As shown, the inclination angle α of the first helical teeth 41 ranges from 3-30°, and the inclination angle α of the second helical teeth 42 ranges from 3-30°. For the service life of the groove, pre...
PUM
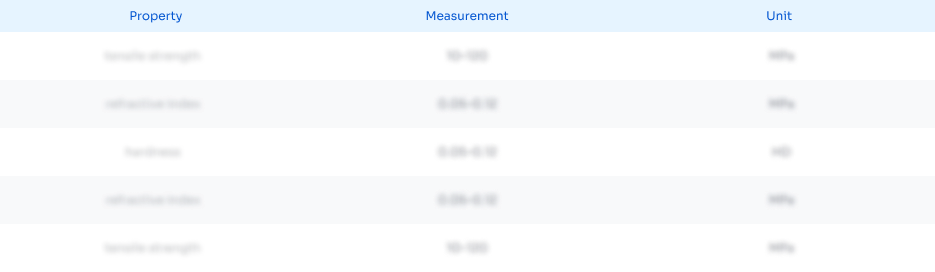
Abstract
Description
Claims
Application Information

- Generate Ideas
- Intellectual Property
- Life Sciences
- Materials
- Tech Scout
- Unparalleled Data Quality
- Higher Quality Content
- 60% Fewer Hallucinations
Browse by: Latest US Patents, China's latest patents, Technical Efficacy Thesaurus, Application Domain, Technology Topic, Popular Technical Reports.
© 2025 PatSnap. All rights reserved.Legal|Privacy policy|Modern Slavery Act Transparency Statement|Sitemap|About US| Contact US: help@patsnap.com