Rubber automatic dipping forming device for rubber band machining
A dipping molding and rubber band technology, which is applied in the field of rubber automatic dipping molding device for rubber band processing, can solve the problems of manual demoulding, lower processing efficiency, low processing efficiency, etc., and achieve the effect of ensuring drying effect and improving lubrication effect
- Summary
- Abstract
- Description
- Claims
- Application Information
AI Technical Summary
Problems solved by technology
Method used
Image
Examples
Embodiment 1
[0039] An automatic rubber dipping and molding device for rubber band processing, comprising a base box 1, a plurality of support feet 2 installed at the lower end of the base box 1, and a processing panel 3 horizontally installed at the upper end of the base box 1, and a support is installed at the upper end of the processing panel 3 Frame 4, and a rotating mechanism 5 is installed on the inner top wall of the supporting frame 4, and the rotating mechanism 5 is used for the circulation of the mold between the dipping box 7, the drying mechanism 8 and the lubricating mechanism 10 in order to ensure that the cylindrical rubber belt c Dip molding and demoulding, the bottom of the rotating mechanism 5 is provided with a lifting plate 6, and the lifting plate 6 is arranged on the upper end surface of the processing panel 3, and the upper end of the lifting plate 6 is provided with a dipping box 7, a drying mechanism 8 and a lubricating mechanism 10 , realizing the lubrication of th...
Embodiment 2
[0058] The difference between this embodiment and embodiment 1 is that, as figure 2 As shown, the upper edge of the lifting plate 6 is also equipped with a plurality of support bases 14, and the lower end of the support base 14 is vertically installed with a telescopic limit rod 13, and the lower end of the telescopic limit rod 13 extends to the inner cavity of the base box 1 And vertically installed on the inner bottom wall of the base box 1, the upper end of the processing panel 3 is provided with a plurality of preset grooves 15 matching with the support seat 14, which effectively play the role of limiting and ensure the horizontal lifting of the lifting plate 6 , so as to carry out rubber automatic dip molding.
[0059] Refer to Example 1 for other undescribed structures.
PUM
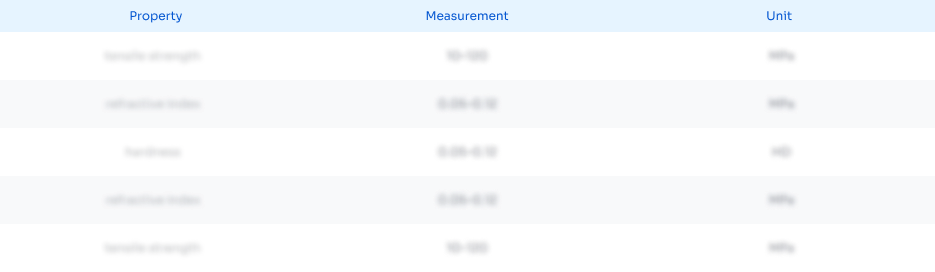
Abstract
Description
Claims
Application Information

- R&D Engineer
- R&D Manager
- IP Professional
- Industry Leading Data Capabilities
- Powerful AI technology
- Patent DNA Extraction
Browse by: Latest US Patents, China's latest patents, Technical Efficacy Thesaurus, Application Domain, Technology Topic, Popular Technical Reports.
© 2024 PatSnap. All rights reserved.Legal|Privacy policy|Modern Slavery Act Transparency Statement|Sitemap|About US| Contact US: help@patsnap.com