Precise adjustment method of satellite-borne instrument equipment
A precision adjustment and instrument technology, applied in design optimization/simulation, complex mathematical operations, etc., can solve problems such as incomplete consideration of factors and low adjustment accuracy, and achieve the effects of reducing labor intensity, improving adjustment efficiency, and improving work efficiency
- Summary
- Abstract
- Description
- Claims
- Application Information
AI Technical Summary
Problems solved by technology
Method used
Image
Examples
specific Embodiment approach 1
[0044] Specific implementation mode one: refer to Figure 5 Specifically illustrate the present embodiment, the precision adjustment method of the spaceborne instrument and equipment described in the present embodiment, comprises the following steps:
[0045] Step 1. Design the theoretical coordinate matrix of all gasket points in the astral coordinate system And obtain the theoretical coordinate matrix of all gasket points in the target cube mirror coordinate system of the tested instrument according to the geometric dimensions of the target cube mirror support structure of the tested instrument
[0046] According to the following formula, the theoretical matrix M of the spatial relationship between the star coordinate system and the target cube mirror coordinate system of the measured instrument is obtained TH :
[0047]
[0048] In this embodiment, Determined by the geometry of the support structure of the cubic mirror is known and fixed, M TH It is a 4th-order h...
specific Embodiment approach 2
[0093] Specific embodiment two: this embodiment is to further explain the precise adjustment method of the spaceborne instrument and equipment described in specific embodiment one. In this embodiment, after step six, the following steps are also included:
[0094] Step 7: Carry out satellite precision measurement again to obtain the actual matrix of the spatial relationship between the new star coordinate system and the target cube mirror coordinate system of the instrument under test
[0095] Step 8. Judgment and the M obtained in step 1 TH Whether the absolute value of the deviation, the absolute value of the angle difference and the absolute value of the position coordinate difference satisfy the following formula, if yes, the fine adjustment in step 6 is valid; otherwise, it is invalid and returns to step 2;
[0096] The absolute value of the angle difference should satisfy the following formula:
[0097]
[0098] alpha X′X 、α X′Y and alpha X′Z Respectively, the i...
specific Embodiment approach 3
[0104] Specific embodiment three: This embodiment is to further explain the precise adjustment method of the spaceborne instrument and equipment described in specific embodiment one. In this embodiment, after determining the adjustment height of each shim, the adjustment of each shim The coordinate matrix is updated:
[0105]
[0106] Then the updated and Comparing and judging whether the adjustment is qualified or not can be judged from the deviation between the two.
PUM
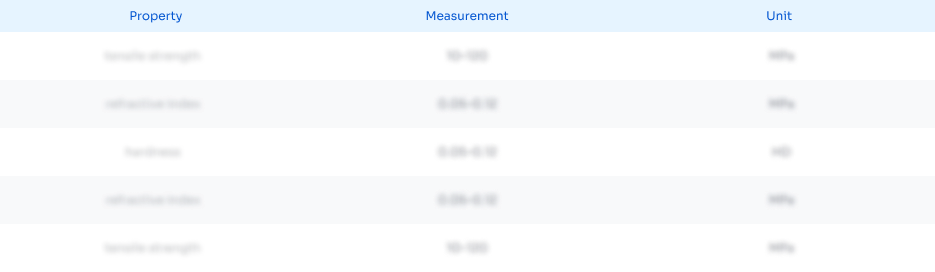
Abstract
Description
Claims
Application Information

- Generate Ideas
- Intellectual Property
- Life Sciences
- Materials
- Tech Scout
- Unparalleled Data Quality
- Higher Quality Content
- 60% Fewer Hallucinations
Browse by: Latest US Patents, China's latest patents, Technical Efficacy Thesaurus, Application Domain, Technology Topic, Popular Technical Reports.
© 2025 PatSnap. All rights reserved.Legal|Privacy policy|Modern Slavery Act Transparency Statement|Sitemap|About US| Contact US: help@patsnap.com