Compact robot variable rigidity joint
A technology of variable stiffness and robotics, applied in the field of robotics, can solve problems such as complex and large structures and difficult breakthroughs in principles, and achieve the effects of compact overall structure, simple appearance, and good interpersonal interaction
- Summary
- Abstract
- Description
- Claims
- Application Information
AI Technical Summary
Problems solved by technology
Method used
Image
Examples
Embodiment Construction
[0023] The present invention will be described in further detail below in conjunction with the accompanying drawings.
[0024] like Figure 1-5 As shown, the present invention includes a drive mechanism 1, a stiffness adjustment mechanism 2 and a variable stiffness unit 3, such as Figure 2~3 As shown, the variable stiffness unit 3 includes an input shaft 314, a connecting frame 315 and an output disk 301, wherein the input shaft 314 is connected to the connecting frame 315, and the output disk 301 is sleeved on the input shaft 314 through a bearing support. A lead screw 306 is provided in the middle of the frame 315, and input support rods 302 are provided on both sides. The lead screw 306 is provided with two screw nuts 316 with opposite helical directions, and each input support rod 302 is provided with two movable The pulley frame 304, and the pulley frame 304 is fixedly connected with the nut 316 on the corresponding side, the rotation of the screw 306 drives the two nut...
PUM
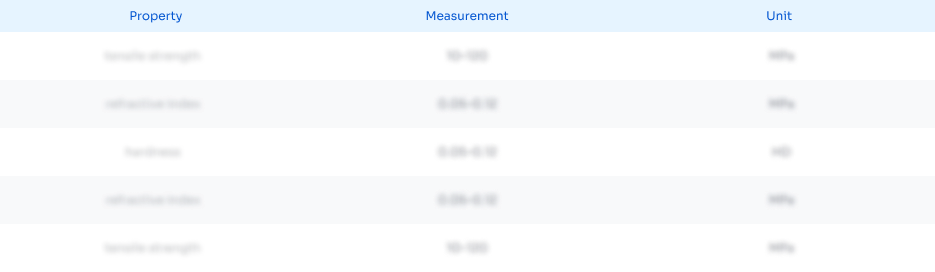
Abstract
Description
Claims
Application Information

- R&D
- Intellectual Property
- Life Sciences
- Materials
- Tech Scout
- Unparalleled Data Quality
- Higher Quality Content
- 60% Fewer Hallucinations
Browse by: Latest US Patents, China's latest patents, Technical Efficacy Thesaurus, Application Domain, Technology Topic, Popular Technical Reports.
© 2025 PatSnap. All rights reserved.Legal|Privacy policy|Modern Slavery Act Transparency Statement|Sitemap|About US| Contact US: help@patsnap.com