Manipulator capable of enhancing clamping force
A technology of manipulator and clamping force, which is applied in the field of manipulators, can solve the problems of increasing the volume of the manipulator, restricting the grasping force of the rope mechanism, and increasing the volume of the driving motor, so as to achieve the effect of improving stability
- Summary
- Abstract
- Description
- Claims
- Application Information
AI Technical Summary
Problems solved by technology
Method used
Image
Examples
Embodiment
[0035] Such as Figure 1 to Figure 11As shown, the manipulator of the present invention that can enhance the clamping force includes two clamping arms, a base 1 and a driving part, wherein the two clamping arms are mirror-symmetrically arranged and connected with the base 1 and the driving part respectively, and the driving part drives The movement of the two clamping arms enables the clamping or opening movement. The driving part is arranged in the base 1, the driving part is connected with a rope 10 and serves as the starting end of the rope 10, and the clamping arm includes a root finger part 2 hinged with the base 1, a last finger part 3, and a Arm clamping or opening movement and locking transmission mechanism for locking the clamping state of the clamping arm. Wherein, the locking transmission mechanism is arranged on the root finger part 2 and is connected with the last finger part 3. The last finger part 3 is hinged with the root finger part 2 and is provided with a p...
PUM
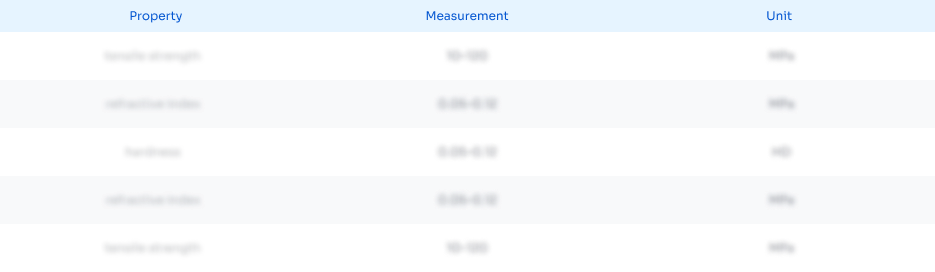
Abstract
Description
Claims
Application Information

- R&D Engineer
- R&D Manager
- IP Professional
- Industry Leading Data Capabilities
- Powerful AI technology
- Patent DNA Extraction
Browse by: Latest US Patents, China's latest patents, Technical Efficacy Thesaurus, Application Domain, Technology Topic, Popular Technical Reports.
© 2024 PatSnap. All rights reserved.Legal|Privacy policy|Modern Slavery Act Transparency Statement|Sitemap|About US| Contact US: help@patsnap.com