Ceiling plastic frame and fabric base material welding device
A technology of welding device and plastic frame, which is applied in the field of automobile decoration, can solve the problems of non-environmental protection, low work efficiency and environmental protection by glue sticking, and achieves the effect of solving low work efficiency and stable sticking quality.
- Summary
- Abstract
- Description
- Claims
- Application Information
AI Technical Summary
Problems solved by technology
Method used
Image
Examples
Embodiment 1
[0027] Such as figure 1 , figure 2 As shown, the ceiling plastic frame and fabric substrate welding device 100 of this embodiment is used to weld and connect the ceiling plastic frame and the fabric substrate. The ceiling plastic frame and fabric substrate welding device 100 includes a frame portion 10 and a clamping portion 20. Two ultrasonic welding parts 30 and a control part 40.
[0028] The frame part 10 includes a bottom bracket 11 and two blocking frames 12.
[0029] The bottom bracket 11 is a rectangular parallelepiped frame body, a rectangular parallelepiped frame structure welded by a plurality of straight rods.
[0030] The cross section of the stopper 12 is in the shape of "[", the two stoppers 12 are respectively arranged opposite to the two ends of the bottom bracket 11, and the openings of the two stoppers 12 are arranged oppositely.
[0031] The clamping part 20 includes a fabric base mold and a plurality of clamping members 21.
[0032] Such as image 3 , Figure 4 As...
Embodiment 2
[0055] The structure in this embodiment is the same as that in the first embodiment, except that in this embodiment, the plastic frame S of the ceiling is replaced with soundproof cotton, and the soundproof cotton and the fabric base material are connected by ultrasonic welding.
[0056] The function and effect of the embodiment
[0057] According to the welding device for the roof plastic frame and the fabric base material according to the present embodiment, because it has a control part and an ultrasonic welding part with a robotic arm and an ultrasonic welding unit, the control part controls the head of the ultrasonic welding gun at a predetermined position of the roof plastic frame Perform ultrasonic welding according to the set procedure to connect the plastic frame of the roof to the fabric base material.
[0058] The welding device for the plastic frame of the ceiling and the fabric base material of this embodiment adopts the automatic welding of the robot arm, which not only...
PUM
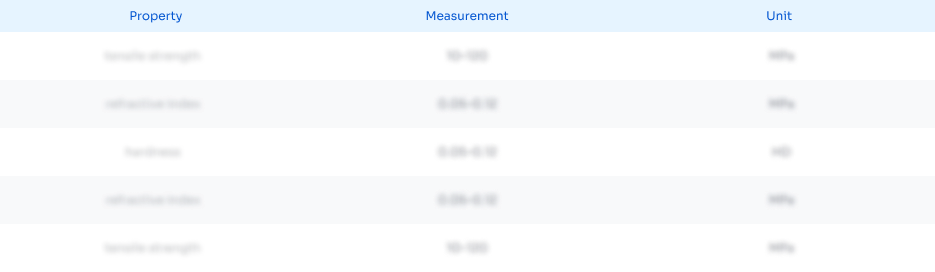
Abstract
Description
Claims
Application Information

- Generate Ideas
- Intellectual Property
- Life Sciences
- Materials
- Tech Scout
- Unparalleled Data Quality
- Higher Quality Content
- 60% Fewer Hallucinations
Browse by: Latest US Patents, China's latest patents, Technical Efficacy Thesaurus, Application Domain, Technology Topic, Popular Technical Reports.
© 2025 PatSnap. All rights reserved.Legal|Privacy policy|Modern Slavery Act Transparency Statement|Sitemap|About US| Contact US: help@patsnap.com