Automatic conveying device for parts among welding stations
A self-conveying and welding station technology, applied in the direction of auxiliary equipment, welding equipment, auxiliary welding equipment, etc., can solve problems such as high cost, hidden safety hazards, and easy fatigue, so as to reduce labor intensity, improve production efficiency, and shorten transportation time Effect
- Summary
- Abstract
- Description
- Claims
- Application Information
AI Technical Summary
Problems solved by technology
Method used
Image
Examples
Embodiment Construction
[0024] Below with reference to the accompanying drawings, through the description of the implementation examples, the specific embodiments of the present invention, such as the shape, structure, mutual position and connection relationship between each part, the role and working principle of each part, etc., will be further described. detailed description of the .
[0025] Such as Figure 1-3 , the self-conveying device for parts between welding stations of the present invention, the key is to include a base 1, a driving cylinder 2 is arranged on the base 1, a conveying platform is arranged on the driving cylinder 2, and the conveying platform 3 is connected with the piston rod in the driving cylinder 2 , the conveyor table 3 comprises a conveyor table lower bracket 31 and a conveyor table front end bracket 32, the conveyor table lower bracket 31 is provided with a load-bearing pillar 311 for supporting the bottom of the workpiece A, and the top of the conveyor table front end ...
PUM
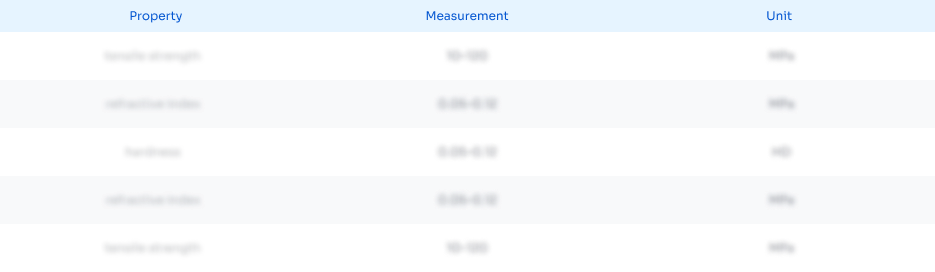
Abstract
Description
Claims
Application Information

- Generate Ideas
- Intellectual Property
- Life Sciences
- Materials
- Tech Scout
- Unparalleled Data Quality
- Higher Quality Content
- 60% Fewer Hallucinations
Browse by: Latest US Patents, China's latest patents, Technical Efficacy Thesaurus, Application Domain, Technology Topic, Popular Technical Reports.
© 2025 PatSnap. All rights reserved.Legal|Privacy policy|Modern Slavery Act Transparency Statement|Sitemap|About US| Contact US: help@patsnap.com