Motor fault detection system based on high-frequency signal coupling injection
A high-frequency signal, fault detection technology, applied in the direction of motor generator testing, measuring electricity, electromechanical devices, etc., can solve problems such as misjudgment of motor faults, and achieve the effect of expanding the scope of application and overcoming the slow response to faults.
- Summary
- Abstract
- Description
- Claims
- Application Information
AI Technical Summary
Problems solved by technology
Method used
Image
Examples
Embodiment Construction
[0038] A motor fault detection system based on high-frequency signal coupling injection of the present invention will be described in detail below with reference to the embodiments and drawings.
[0039] A motor fault detection system based on high-frequency signal coupling injection of the present invention generates a high-frequency detection signal through an independent signal source, and simultaneously injects the high-frequency detection signal and the drive voltage output by the inverter into the motor winding through a coupling circuit. The two frequency division multiplexes the motor windings without interfering with each other. The high-frequency detection signal is used for online detection of motor faults, and the low-frequency drive voltage is used to control the normal operation of the motor. High frequency current or voltage responses are obtained by signal processing circuits. In practical applications, the generation method, waveform selection, injection metho...
PUM
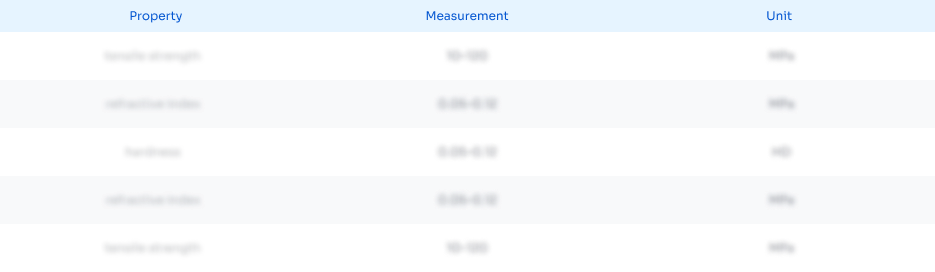
Abstract
Description
Claims
Application Information

- Generate Ideas
- Intellectual Property
- Life Sciences
- Materials
- Tech Scout
- Unparalleled Data Quality
- Higher Quality Content
- 60% Fewer Hallucinations
Browse by: Latest US Patents, China's latest patents, Technical Efficacy Thesaurus, Application Domain, Technology Topic, Popular Technical Reports.
© 2025 PatSnap. All rights reserved.Legal|Privacy policy|Modern Slavery Act Transparency Statement|Sitemap|About US| Contact US: help@patsnap.com