Waste incineration system and high-efficiency incineration control method
A waste incineration and waste technology, applied in the direction of combustion methods, incinerators, combustion types, etc., can solve the problems of poor utilization of heat and combustible gas, dioxin emission beyond the standard, unfavorable energy saving, etc., to facilitate subsequent tail gas treatment, Effects of saving water and preventing resynthesis of dioxins
- Summary
- Abstract
- Description
- Claims
- Application Information
AI Technical Summary
Problems solved by technology
Method used
Image
Examples
Embodiment 1
[0049] see Figure 1-8 , a waste incineration system, which includes a primary combustion chamber 2 for primary incineration of waste, the flue gas outlet of the primary combustion chamber 2 communicates with the flue gas inlet of the secondary combustion chamber 4 through the first flue 15, and the two The flue gas outlet of the secondary combustion chamber 4 is connected to the spray tower 6 for flue gas spraying treatment through the second flue 19, and the top outlet of the spray tower 6 is connected to the flue gas purification system through the third flue 7 . By adopting the incineration system with the above-mentioned structure, it can be used for incineration treatment of garbage, overcomes the shortcomings of existing garbage carbonization incineration treatment equipment, can effectively control the temperature of garbage carbonization and utilize the combustible gas energy after carbonization, and control the combustion temperature of tail gas and smoke at the same...
Embodiment 2
[0062] Such as Figure 9-10 , the high-efficiency incineration control method of the waste incineration system, it comprises the following steps:
[0063] Step 1: Preparation, system self-inspection, power on, voltage, leakage, safety protection system self-inspection, after the self-inspection is normal, enter the second step;
[0064] Step 2: the primary combustion chamber 2 and the secondary combustion chamber 4 heat up the combustion chamber, and during the heating process, the spray tower 6 is opened to cool down the flue gas generated by combustion;
[0065] Step 3: Convey and fill the garbage, put the garbage into the primary combustion chamber 2 through the conveying device 1 and evenly distribute the material, close the feeding door 204, the garbage starts to burn, and the first temperature sensor 3 of the primary combustion chamber 2 monitors the temperature of the flue gas generated by combustion , the temperature of the primary combustion chamber 2 is controlled, ...
Embodiment 3
[0072] In the present embodiment, the main parameters of the adopted primary combustion chamber 2 are:
[0073] The amount of air needed to burn 200kg / h of domestic waste: 405.3m 3 / h;
[0074] The total flue gas volume produced by tenderly burning 200kg / h domestic waste: 573.84m 3 / h;
[0075] The amount of natural gas required to burn 200kg / h of domestic waste: 6.57m 3 / h;
[0076] Air volume required for natural gas combustion: 75.06m 3 / h;
[0077] Primary combustion chamber burner model: Baide BTG15 ME;
[0078] Burner motor power: 0.18kW;
[0079] Blower model and its motor power: HTB75-032 0. 3kW;
[0080] Primary combustion chamber heat loss: 30%;
[0081] The total displacement of the primary combustion chamber: 655.468m 3 / h;
[0082] Make the exhaust temperature of the primary combustion chamber of the furnace: 700°C;
[0083] The main parameters of the adopted secondary combustion chamber 4 are:
[0084] Amount of exhaust gas entering the secondary com...
PUM
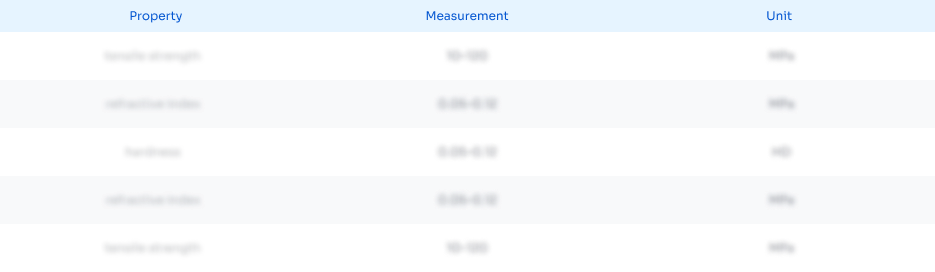
Abstract
Description
Claims
Application Information

- Generate Ideas
- Intellectual Property
- Life Sciences
- Materials
- Tech Scout
- Unparalleled Data Quality
- Higher Quality Content
- 60% Fewer Hallucinations
Browse by: Latest US Patents, China's latest patents, Technical Efficacy Thesaurus, Application Domain, Technology Topic, Popular Technical Reports.
© 2025 PatSnap. All rights reserved.Legal|Privacy policy|Modern Slavery Act Transparency Statement|Sitemap|About US| Contact US: help@patsnap.com