Gap bridging system
A gap and bridging technology, applied in the direction of vehicle components, pedals or ladders, railway car body components, etc., can solve problems such as pedal skew, drive device or control electronic device layout difficulties, etc., to achieve small force and realize structural space Gain, skew prevention effect
- Summary
- Abstract
- Description
- Claims
- Application Information
AI Technical Summary
Problems solved by technology
Method used
Image
Examples
Embodiment Construction
[0017] figure 1 The principle of a gap bridging system is shown exemplarily and schematically. Shown in a highly abstract view is a gap bridging system 1 comprising a linearly slidable supported pedal 3 . The pedal 3 is slidably supported by means of a sliding bearing consisting of two sliding bearing-linear guides 5 and a rolling bearing-linear guide 4 . The sliding bearing-linear guide 5 is designed here as a floating bearing and transmits the forces between the pedal and the component carrier 2 or the carriage only in the vertical direction, the rolling bearing-linear guide 4 then transmits the force between the pedal and the component carrier 2 or the carriage. The forces between the component brackets 2 are transmitted in all spatial directions except the extension direction of the pedal 3 . Apart from the running board 1 and the linear guides 4 , 5 , the gap bridging system 1 also includes a component carrier 2 , via which the gap bridging system 1 can be connected to ...
PUM
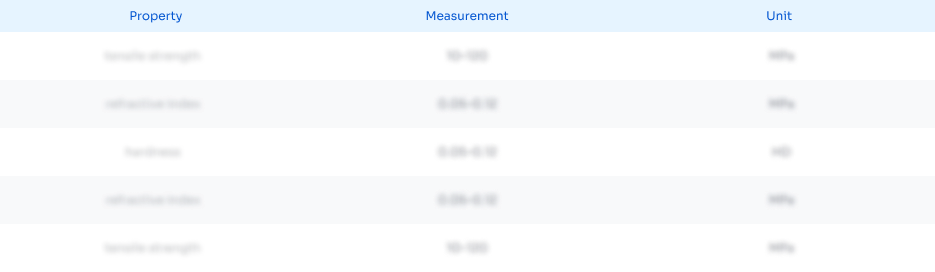
Abstract
Description
Claims
Application Information

- R&D Engineer
- R&D Manager
- IP Professional
- Industry Leading Data Capabilities
- Powerful AI technology
- Patent DNA Extraction
Browse by: Latest US Patents, China's latest patents, Technical Efficacy Thesaurus, Application Domain, Technology Topic, Popular Technical Reports.
© 2024 PatSnap. All rights reserved.Legal|Privacy policy|Modern Slavery Act Transparency Statement|Sitemap|About US| Contact US: help@patsnap.com