Weight carrying robot for platform scale measurement detection
A handling robot, measurement and detection technology, applied in the field of robots, can solve the problems of high labor intensity and low work efficiency, and achieve the effect of ensuring grasping
- Summary
- Abstract
- Description
- Claims
- Application Information
AI Technical Summary
Problems solved by technology
Method used
Image
Examples
Embodiment 1
[0036] Embodiment 1. Cylinder connecting rod type double gripper
[0037] Including: a base 11, a first cylinder 12 fixed on the base, a second cylinder 13, a right clamp 141 connected with the first cylinder 12, a left clamp 142 connected with the second cylinder 13, and a guide rod 15 , the middle part of the guide rod 15 is fixedly connected to the bottom of the base 11, and the two ends of the guide rod 15 are connected to the respective fixed parts of the left clamp 142 and the right clamp 141; the left clamp 142 and the right clamp 141 are normally in an open state; when When the push rods of the first cylinder 12 and the second cylinder 13 are stretched out under the control of the motion controller, the corresponding right clamp 141 and left clamp 142 turn into a closed state.
[0038] In order to prevent the weight from rotating during transportation, such as image 3 As shown, the cylinder connecting rod type double gripper of the present invention also includes: a ...
Embodiment 2
[0048] Embodiment 2: Press the L-shaped hook on the top of the cylinder
[0049] Such as Figure 5 As shown, the L-shaped hook includes two parts: a body 21 and a hook body 22, and the hook body 22 is provided with a V-shaped groove.
[0050] In order to prevent the weight from slipping and shaking on the manipulator during the subsequent operation of the weight, the L-shaped hook of this embodiment also includes: a fourth cylinder 23 fixedly connected to the L-shaped hook body 22, the fourth cylinder 23 is on the same side as the hook body 22, and also includes a C-shaped pressing block 24 connected with the push rod of the fourth cylinder 23. The upper surface of the lock-shaped weight is in close contact, and the handle of the lock-shaped weight is fixed on the hook.
[0051] Normally, the claws are in a loose state, the cylinder piston push rod is in a retracted state, and the gap between the end of the C-shaped briquetting block and the L-shaped hook is relatively large...
Embodiment 3
[0056] Embodiment 3: Compress C-shaped hooks on both sides of the cylinder
[0057] Such as Figure 7 As shown, the C-shaped hook includes two parts, a body 31 and a hook body 32, and the hook body is provided with a V-shaped groove.
[0058] In order to prevent the weight from slipping and shaking on the mechanical claw when the weight is subsequently operated, the C-shaped hook of this embodiment also includes: a bracket 33 fixedly connected to the top of the C-shaped hook, and the bracket 33 is fixed with a second Five cylinders 34, the sixth cylinder 35, the push rod of the fifth cylinder 34 is connected with the first push rod 36 by the first connecting rod, the push rod of the sixth cylinder 35 is connected with the second push rod 37 by the second connecting rod, The motion controller controls the fifth cylinder 34 and the sixth cylinder 35 to control the telescopic action of push rods respectively, and controls the distance between the first push rod 36 and the second...
PUM
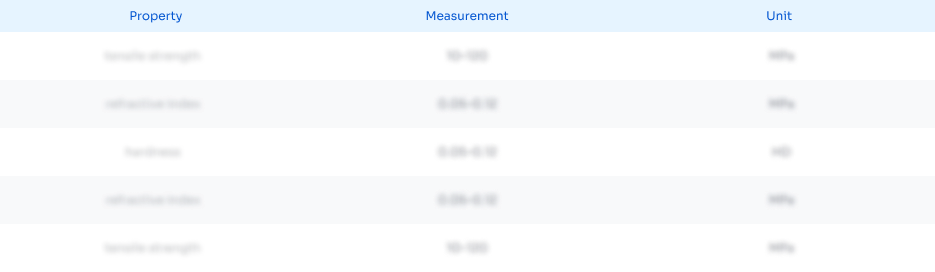
Abstract
Description
Claims
Application Information

- R&D
- Intellectual Property
- Life Sciences
- Materials
- Tech Scout
- Unparalleled Data Quality
- Higher Quality Content
- 60% Fewer Hallucinations
Browse by: Latest US Patents, China's latest patents, Technical Efficacy Thesaurus, Application Domain, Technology Topic, Popular Technical Reports.
© 2025 PatSnap. All rights reserved.Legal|Privacy policy|Modern Slavery Act Transparency Statement|Sitemap|About US| Contact US: help@patsnap.com