To-ground aiming mechanism used for space camera
A space camera and component technology, applied in the field of aerospace remote sensing, can solve the problems of high power consumption and poor maneuverability, and achieve the effects of low power consumption, good maneuverability and fast adjustment speed
- Summary
- Abstract
- Description
- Claims
- Application Information
AI Technical Summary
Problems solved by technology
Method used
Image
Examples
specific Embodiment approach 1
[0027] Specific implementation mode one: combine Figure 1-5 Describe the present embodiment, a space camera ground aiming mechanism, which includes a space camera 100, a satellite platform 101 and a mechanism body arranged between the space camera and the satellite platform, the mechanism body includes a shaft assembly, a feedback assembly and A drive assembly that controls the movement of the shafting assembly, wherein the shafting assembly includes a turntable 1, a fixed inner shaft 2 and a base 3, the fixed inner shaft 2 has a ring structure and one end is fixed on the base 3, so The turntable 1 is rotatably set on the fixed inner shaft 2, the top of the turntable 1 is fixedly connected to the space camera 100 through the adapter 17, and the base 3 is fixedly connected to the satellite platform 101.
[0028] The feedback assembly includes a moving inner shaft 5, a photoelectric encoder 6 and a fixed flange 7, the moving inner shaft 5 is installed in the fixed inner shaft 2...
PUM
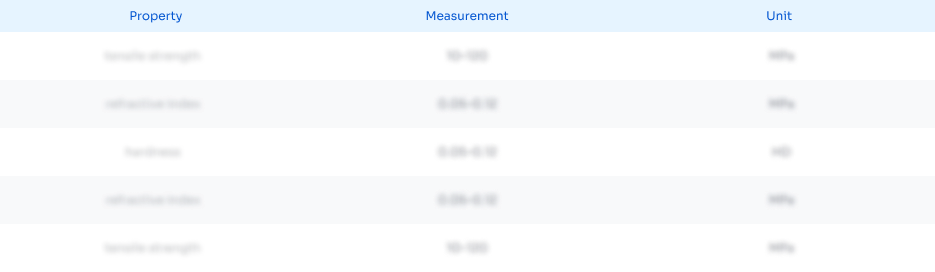
Abstract
Description
Claims
Application Information

- Generate Ideas
- Intellectual Property
- Life Sciences
- Materials
- Tech Scout
- Unparalleled Data Quality
- Higher Quality Content
- 60% Fewer Hallucinations
Browse by: Latest US Patents, China's latest patents, Technical Efficacy Thesaurus, Application Domain, Technology Topic, Popular Technical Reports.
© 2025 PatSnap. All rights reserved.Legal|Privacy policy|Modern Slavery Act Transparency Statement|Sitemap|About US| Contact US: help@patsnap.com