Strain wave gear mechanism with inner seal
A technology of gear mechanism and inner seal, which is applied to the sealing of engines, belts/chains/gears, manipulators, etc., and can solve problems such as lubricant leakage and premature dry operation of gear mechanisms
- Summary
- Abstract
- Description
- Claims
- Application Information
AI Technical Summary
Problems solved by technology
Method used
Image
Examples
Embodiment Construction
[0045] figure 1 A first exemplary embodiment of a stress wave gear mechanism 1 is shown, which has a gear mechanism component CS configured as an internal gear, which in the region of its internal toothing 8 overlaps the external toothing 9 of the transmission component FS and Engage regionally. The transmission component FS is connected in a rotationally fixed manner to the inner bearing ring 6 of the swivel bearing 30 , which mounts the transmission component FS and the gear mechanism component CS rotatably relative to each other. The outer bearing ring 5 of the swivel bearing 30 is connected in a rotationally fixed manner to the gear train component CS. Like the transmission component FS, a plug 41 is provided in a rotationally fixed manner, which enables the positioning of the stress wave gear 1 relative to the stress wave gear 1 . figure 1 The output side on the right is blocked.
[0046] Along the transmission axis 26 , about which the components of the stress wave ge...
PUM
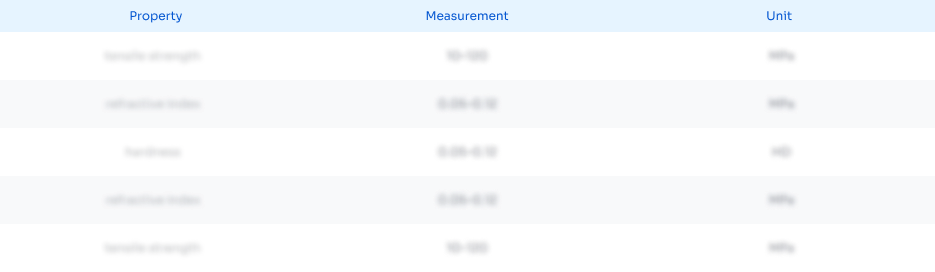
Abstract
Description
Claims
Application Information

- R&D
- Intellectual Property
- Life Sciences
- Materials
- Tech Scout
- Unparalleled Data Quality
- Higher Quality Content
- 60% Fewer Hallucinations
Browse by: Latest US Patents, China's latest patents, Technical Efficacy Thesaurus, Application Domain, Technology Topic, Popular Technical Reports.
© 2025 PatSnap. All rights reserved.Legal|Privacy policy|Modern Slavery Act Transparency Statement|Sitemap|About US| Contact US: help@patsnap.com