Front auxiliary frame aluminum alloy mounting support and vehicle
A technology of front subframe and mounting bracket, which is applied to vehicle components, transportation and packaging, and substructure, etc., to achieve the effect of simple structure, high dimensional accuracy, and improved rigidity
- Summary
- Abstract
- Description
- Claims
- Application Information
AI Technical Summary
Problems solved by technology
Method used
Image
Examples
Embodiment Construction
[0022] The present invention will be described in detail below in conjunction with the accompanying drawings.
[0023] see figure 2 with Figure 7 , the shown front sub-frame aluminum alloy mounting bracket is located between the front sub-frame 1 and the cabin side beam 2, including a bracket body 3 made of aluminum alloy, and the bracket body 3 is a rectangle penetrating in the up and down direction The cylindrical hollow body is provided with X-shaped ribs 7 inside the cavity, and the X-shaped ribs 7 extend along the axial direction of the rectangular cylindrical hollow body, ensuring the structural strength of the bracket body 3 and improving the rigidity of the installation point .
[0024] The upper edge of the bracket body 3 is provided with an upwardly extending connecting plate 4, and a reinforcing plate 5 is fixedly connected to the opposite side of the bracket body 3 and the connecting plate 4. The two opposite sides of the beam 2 are fixedly connected. The int...
PUM
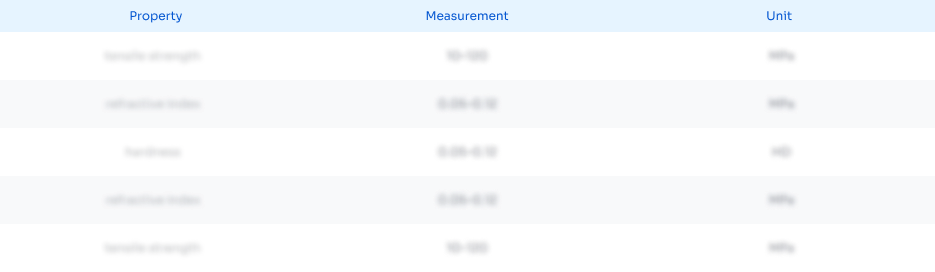
Abstract
Description
Claims
Application Information

- Generate Ideas
- Intellectual Property
- Life Sciences
- Materials
- Tech Scout
- Unparalleled Data Quality
- Higher Quality Content
- 60% Fewer Hallucinations
Browse by: Latest US Patents, China's latest patents, Technical Efficacy Thesaurus, Application Domain, Technology Topic, Popular Technical Reports.
© 2025 PatSnap. All rights reserved.Legal|Privacy policy|Modern Slavery Act Transparency Statement|Sitemap|About US| Contact US: help@patsnap.com