Constant volume diaphragm type filter press
A filter press and diaphragm-type technology, applied in the field of filter presses, can solve the problems of reducing production efficiency, threats to operators, liquid splashing, etc., and achieve the effects of improving production efficiency, avoiding physical hazards, and avoiding material liquid splashing
- Summary
- Abstract
- Description
- Claims
- Application Information
AI Technical Summary
Problems solved by technology
Method used
Image
Examples
Embodiment Construction
[0028] The present invention will be further described below in conjunction with the accompanying drawings and specific embodiments, but not as a limitation of the present invention.
[0029] to combine Figure 1 to Figure 4 As shown, a constant volume diaphragm filter press of a preferred embodiment is shown, which is characterized in that it includes:
[0030] first support 1;
[0031] The second bracket 2, the second bracket 2 is located on the side facing the first bracket 1;
[0032] Clamping screw 3, several clamping screws 3 are arranged between the first bracket 1 and the second bracket 2, and the two ends of the clamping screw 3 are fixedly connected with the first bracket 1 and the second bracket 2 respectively;
[0033] A positioning block 4, each clamping screw 3 is provided with a positioning block 4 at one end close to the first bracket 1;
[0034] A filter press unit 5, several filter press units 5 are sequentially arranged between the first support 1 and the...
PUM
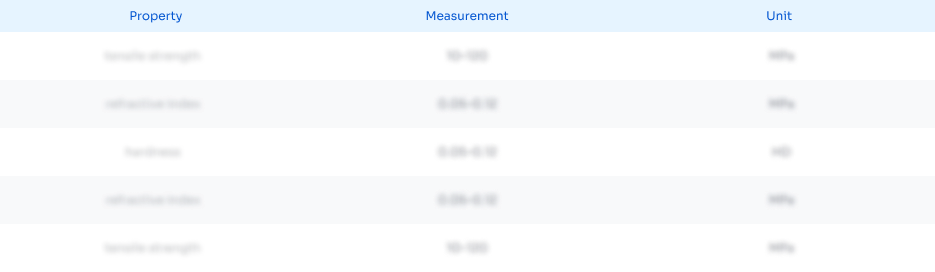
Abstract
Description
Claims
Application Information

- R&D
- Intellectual Property
- Life Sciences
- Materials
- Tech Scout
- Unparalleled Data Quality
- Higher Quality Content
- 60% Fewer Hallucinations
Browse by: Latest US Patents, China's latest patents, Technical Efficacy Thesaurus, Application Domain, Technology Topic, Popular Technical Reports.
© 2025 PatSnap. All rights reserved.Legal|Privacy policy|Modern Slavery Act Transparency Statement|Sitemap|About US| Contact US: help@patsnap.com