Driving axle housing waste automatic disassembling device and method
A technology for automatic disassembly and drive axle housing, which is applied in auxiliary devices, plasma welding equipment, program control manipulators, etc., can solve the problems of failure to automatically disassemble different types of drive axle housing waste, potential safety hazards, and low production efficiency. Achieve the effect of eliminating manual unloading process, high production efficiency and high work efficiency
- Summary
- Abstract
- Description
- Claims
- Application Information
AI Technical Summary
Problems solved by technology
Method used
Image
Examples
Embodiment 1
[0075] An automatic dismantling device for drive axle housing waste, including a horizontal hanging device 11, a lifting connection device 12, and a material unloading device 13;
[0076] The horizontal hanging device 11 includes a beam 111, an inductor mounting support 112, an inductor I113, a buffer 114, a sliding table 115, a vertical boom 116, a guide rail I118, a rodless cylinder 119, and a slider I1110; wherein:
[0077] The beam 111 is fixed above the workbench through the fixing block 1111, and the two guide rails I118 are respectively fastened on both sides of the bottom of the beam 111. The guide rails I118 are external double-axis linear square guide rails (standard parts); the described The slider I1110 is slidingly connected with the guide rail I118, the slider I1110 is a high-speed double-roller slide rail slider table (standard part), and the slider I1110 is fixedly connected with the slide table 115; the rodless cylinder 119 is fixed on the bottom of the beam B...
Embodiment 2
[0085] A method for automatically removing drive axle housing waste, the method comprising the steps of:
[0086] S1. Preparation: Clamp the workpiece in place, slide the rodless cylinder in place along -X, and slide the servo electric cylinder in place along -Y; the specific content of this step S1 is:
[0087] Transfer the workpiece drive axle housing 5 with the pre-machined hole 53 to the workpiece clamping positioner 4, the workpiece clamping positioner clamps the workpiece and turns it in place, and ensures the pre-processed hole 53 each time the workpiece is clamped Always maintain a fixed position, so that the unloading device 13 can accurately extend into the pre-processed hole 53 every time, and will not interfere with the device due to differences in workpieces; the signal is input to the automatic removal device 1 for drive axle housing waste, and the rodless cylinder 119 Work, push the sliding table 115 to move in the -X direction, when the end surface of the slidi...
PUM
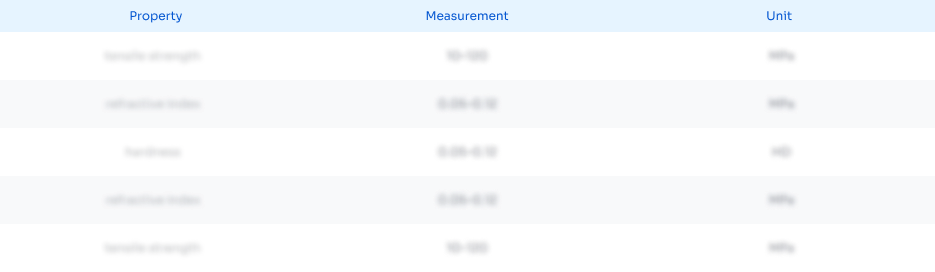
Abstract
Description
Claims
Application Information

- R&D Engineer
- R&D Manager
- IP Professional
- Industry Leading Data Capabilities
- Powerful AI technology
- Patent DNA Extraction
Browse by: Latest US Patents, China's latest patents, Technical Efficacy Thesaurus, Application Domain, Technology Topic, Popular Technical Reports.
© 2024 PatSnap. All rights reserved.Legal|Privacy policy|Modern Slavery Act Transparency Statement|Sitemap|About US| Contact US: help@patsnap.com