Hedge shears
A hedge and scissor blade technology, applied in the direction of trimming hedge equipment, applications, cutting tools, etc., can solve the problems of inability to prevent impact loads, limit the service life of the slip ring transmission mechanism, etc., and achieve improved operability, light weight and light weight. effect of noise
- Summary
- Abstract
- Description
- Claims
- Application Information
AI Technical Summary
Problems solved by technology
Method used
Image
Examples
Embodiment Construction
[0020] The hedge shears 10 shown in Fig. 1 has a shell 12, with a first handle 11 and a second handle 13 on the shell 12, the first handle 11 has a button 9 of an electric working switch not shown in the figure, longitudinally from the shell to the front Extend the hedge shear blade pairs 14, 15. This pair of blades 14, 15 is driven to and fro by an unrepresented motor mounted in the housing 12. The rotary motion of motor shaft 16 is transformed into the reciprocating motion of hedge shear blades 14,15 by motor driving pinion 18 and by slip ring transmission mechanism 20 shown in Fig. 2,4 or 6.
[0021] As can be clearly seen from the exploded view of the slip ring transmission mechanism 20 shown in FIG. 2 , the ends of the hedge shears blades 14 , 15 on the side where the housing is located are connected with the slip ring tool holders 22 , 23 . The tool holders 22, 23 are mounted directly adjacent to each other. When the hedge shears 10 are in operation, their inner planar...
PUM
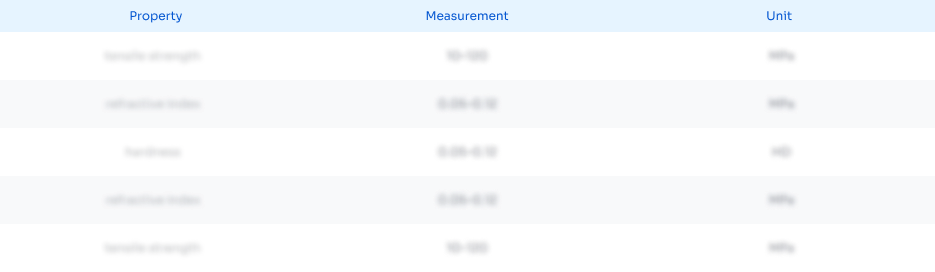
Abstract
Description
Claims
Application Information

- R&D
- Intellectual Property
- Life Sciences
- Materials
- Tech Scout
- Unparalleled Data Quality
- Higher Quality Content
- 60% Fewer Hallucinations
Browse by: Latest US Patents, China's latest patents, Technical Efficacy Thesaurus, Application Domain, Technology Topic, Popular Technical Reports.
© 2025 PatSnap. All rights reserved.Legal|Privacy policy|Modern Slavery Act Transparency Statement|Sitemap|About US| Contact US: help@patsnap.com