Space positioning error measuring device and measuring method thereof
A technology of error measurement and spatial positioning, which is applied in the field of robotics, can solve the problems of inapplicable robot in-position error real-time measurement, positioning device error measurement, and large positioning error size, etc., to achieve simple structure, high precision, and simple error measurement method Effect
- Summary
- Abstract
- Description
- Claims
- Application Information
AI Technical Summary
Problems solved by technology
Method used
Image
Examples
Embodiment 1
[0040] Such as Figure 1-2 As shown, the spatial positioning error measurement device and its measurement method include X rods, Y rods, Z rods, X rods, Y rods, X rods, Y rods, The Z rods are respectively equipped with high-precision laser ranging sensors for measuring the distance from the origin of the coordinate system to the bottom measurement reference surface 6, the left measurement reference surface 2, and the rear measurement reference surface 10, wherein the bottom measurement reference surface 6 is a horizontal plane , the left measurement reference surface 2 and the rear measurement reference surface 10 are two vertical surfaces perpendicular to each other and perpendicular to the bottom measurement reference surface;
[0041] The X-axis horizontal inclination sensor 7 and the Y-axis horizontal inclination sensor 4 are respectively connected to the X-axis horizontal inclination angle sensor 4 for measuring the horizontal inclination angle of the x and y coordinate a...
Embodiment 2
[0048] The measuring method of space positioning error measuring device, on the basis of embodiment 1, comprises the following steps:
[0049] (1) The transformation relationship between the measurement coordinate system {M} and the world coordinate system {W} is expressed as:
[0050]
[0051] Among them, T x (x M ), T y (y M ), T z (z M ) are respectively the homogeneous matrix of {W} to {M} moving transformation, P z (ψ), R y″ (θ) are the homogeneous matrices of {M} successively rotating and transforming around the z axis, x' axis and y" axis;
[0052]
[0053]
[0054]
[0055] (2) Obtain the angle ψ that the measurement coordinate system {M} rotates around the z-axis through the magnetic field direction sensor 1, that is, ∠bO M b';
[0056] (3) Obtain the angle that the measurement coordinate system {M} rotates around the x' axis through the Y-axis horizontal inclination sensor 4 That is, ∠b″O M b';
[0057] (4) The angle α between the zx coordi...
Embodiment 3
[0065] On the basis of Embodiment 2, under ideal conditions, the x, y, z coordinate axes of the measurement coordinate system {M} are orthogonal to the zy, zx, xy planes of the reference world coordinate system and three points a, b, and c respectively. Due to the positioning error of the robot base on the secondary positioning device, the measuring device deflects following the robot base, and the result of the deflection is expressed in Euler angles: the measurement coordinate system rotates around the z-axis by ψ, and around the x-axis Rotate θ around the y-axis to get the final state. The x, y, and z coordinate axes of the final measurement coordinate system {M} are orthogonal to the zy, zx, and xy planes of the reference world coordinate system and the three points a", b", and c". The measurement coordinate system {M} is relative to The Euler rotation representation of the world coordinate system {W}, that is, the formula (1);
[0066] image 3 In the rotation transfor...
PUM
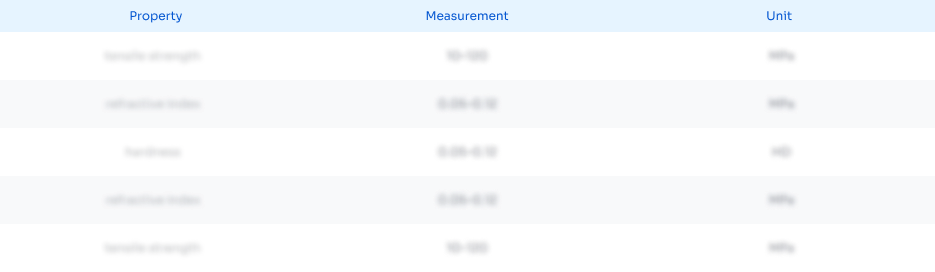
Abstract
Description
Claims
Application Information

- R&D
- Intellectual Property
- Life Sciences
- Materials
- Tech Scout
- Unparalleled Data Quality
- Higher Quality Content
- 60% Fewer Hallucinations
Browse by: Latest US Patents, China's latest patents, Technical Efficacy Thesaurus, Application Domain, Technology Topic, Popular Technical Reports.
© 2025 PatSnap. All rights reserved.Legal|Privacy policy|Modern Slavery Act Transparency Statement|Sitemap|About US| Contact US: help@patsnap.com