Modular ground crawling software robot
A modular and robotic technology, applied in the field of robotics, can solve problems such as poor safety and human interaction, difficulty in rigid robots, and low environmental adaptability, and achieve the effects of strong replaceability, strong repeatability, and strong adaptability
- Summary
- Abstract
- Description
- Claims
- Application Information
AI Technical Summary
Problems solved by technology
Method used
Image
Examples
Embodiment 1
[0051] Such as figure 1 As shown, a modular ground crawling soft robot, including:
[0052] The second pneumatic telescopic unit 2 is configured to bend or extend along its own axis when inflated;
[0053] The first pneumatic telescopic unit 1 is symmetrically connected to both ends of the second pneumatic telescopic unit 2; it is set so that it can only extend in one direction along its own axial direction when inflated, and each of the first pneumatic telescopic units 1 The extension directions are the same and perpendicular to the axial direction of the second pneumatic telescopic unit 2 .
[0054] Such as image 3 As shown, the second pneumatic telescopic unit 2 includes:
[0055] The second axially telescopic main body 21 is cylindrical as a whole, made of flexible material and has two closed air cavities symmetrically inside, such as Figure 7 shown;
[0056] A plurality of rigid restricting rings are evenly spaced on the outer peripheral wall of the second axially ...
Embodiment 2
[0070] Such as Figure 11 As shown, the difference between this embodiment and Embodiment 1 is that: the two ends of the second pneumatic telescopic unit 2 are respectively connected with the second connectors 4, the number of the first pneumatic telescopic units 1 is four, and the four The second connectors 4 are symmetrically connected in pairs on the left and right sides of the two second connectors 4 respectively. In this embodiment, four first pneumatic telescopic units 1 are provided to improve the stability of the robot during movement.
[0071] Such as Figure 12 As shown, the second connector 4 includes a square tubular main body, the two vertical edges of the left and right panels of the square tubular main body are extended with second flanges 41, and the left and right panels of the square tubular main body are The inner side of the square tubular body is vertically provided with two fourth slots 44 which are respectively located in the front panel of the square t...
Embodiment 3
[0073] Such as Figure 13 As shown, the difference between the present embodiment and the second embodiment is that there are two second pneumatic telescopic units 2, and the adjacent second pneumatic telescopic units 2 are connected in series through the first connecting piece 3, such as Figure 14 As shown, the front and rear ends of the first connector 3 are provided with a first U-shaped hole 32 and a second card slot 31 that is plugged and fitted with the first flange 23 of the connector 22. The first connector The left and right sides of the component 3 are provided with third card slots 33 . In this embodiment, the speed of linear motion can be effectively increased by connecting two second pneumatic telescopic units 2 in series.
PUM
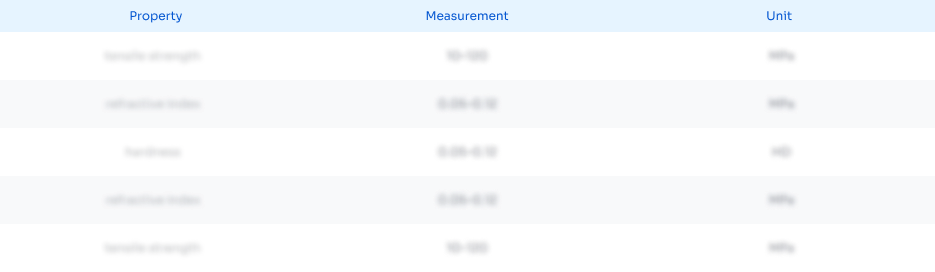
Abstract
Description
Claims
Application Information

- Generate Ideas
- Intellectual Property
- Life Sciences
- Materials
- Tech Scout
- Unparalleled Data Quality
- Higher Quality Content
- 60% Fewer Hallucinations
Browse by: Latest US Patents, China's latest patents, Technical Efficacy Thesaurus, Application Domain, Technology Topic, Popular Technical Reports.
© 2025 PatSnap. All rights reserved.Legal|Privacy policy|Modern Slavery Act Transparency Statement|Sitemap|About US| Contact US: help@patsnap.com