Forming device and tire forming method
A molding device and molding tooling technology, applied in the field of tire manufacturing, can solve the problems of wasted space of the whole machine, the number of operators is large, and the equipment occupies a large area, so as to improve the cost performance of the equipment, improve the operation area, and reduce the floor space. Effect
- Summary
- Abstract
- Description
- Claims
- Application Information
AI Technical Summary
Problems solved by technology
Method used
Image
Examples
Embodiment Construction
[0046] Below in conjunction with accompanying drawing and specific embodiment the present invention will be described in further detail:
[0047] see image 3 , a forming device disclosed in the present invention, comprising a horizontal and vertical orthogonal track unit 4, a transfer mechanism, a carcass fitting unit, a bead placement unit 5, a belt layer fitting unit, a forming unit, a shaping unit and a tire unloading mechanism 19. Wherein the carcass fitting unit includes carcass fitting tooling 2, carcass fitting tooling power system 1, carcass fitting tooling rolling mechanism 3 and host feeding system 8; the belt layer fitting unit includes belt layer fitting tooling 15, Belt laminating tooling power system 16, belt laminating tooling rolling mechanism and auxiliary machine feeding system 17; forming unit includes forming tooling 9, forming tooling power system 10 and forming tooling rolling mechanism 11; shaping unit includes The shaping tool 12, the shaping tool po...
PUM
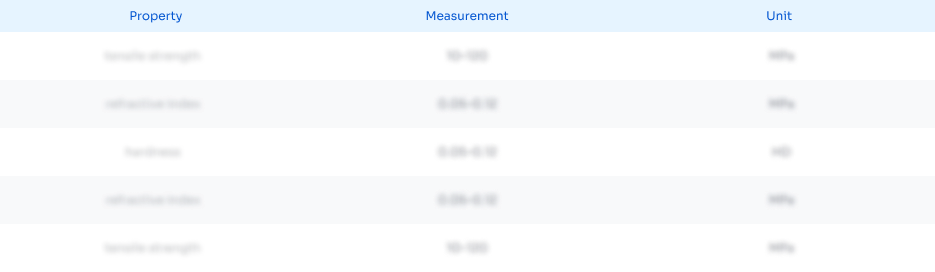
Abstract
Description
Claims
Application Information

- R&D
- Intellectual Property
- Life Sciences
- Materials
- Tech Scout
- Unparalleled Data Quality
- Higher Quality Content
- 60% Fewer Hallucinations
Browse by: Latest US Patents, China's latest patents, Technical Efficacy Thesaurus, Application Domain, Technology Topic, Popular Technical Reports.
© 2025 PatSnap. All rights reserved.Legal|Privacy policy|Modern Slavery Act Transparency Statement|Sitemap|About US| Contact US: help@patsnap.com