Manufacturing method for conical box body structural member
A manufacturing method and a technology for structural parts, which are applied in the field of manufacturing conical box structural parts, can solve the problems of difficult welding deformation, many weld seams, and high precision requirements for conical box structural parts, and achieve convenient welding and reduced deformation Effect
- Summary
- Abstract
- Description
- Claims
- Application Information
AI Technical Summary
Problems solved by technology
Method used
Image
Examples
Embodiment Construction
[0052] In order to make the object, technical solution and advantages of the present invention clearer, the implementation manner of the present invention will be further described in detail below in conjunction with the accompanying drawings.
[0053] In order to facilitate the understanding of the technical solution provided by the embodiment of the present invention, the function and structure of the tapered box structure 84 will be introduced first. The conical box structure 84 is an important load-bearing member of the rotary unit 82, such as figure 1As shown, the upper part of the conical box structure 84 is connected to the brake assembly 83 , and the lower part is connected to the propulsion unit 81 . There is a close cooperation relationship between the tapered box and the rotary shaft of the rotary unit 82 , the rotary bearing (not shown in the figure) and the box cover 85 . The upper cover plate 1 of the conical box structure 84 is installed on the hull, and the we...
PUM
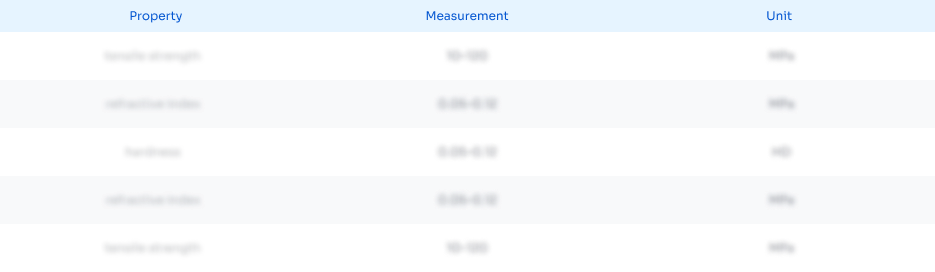
Abstract
Description
Claims
Application Information

- R&D Engineer
- R&D Manager
- IP Professional
- Industry Leading Data Capabilities
- Powerful AI technology
- Patent DNA Extraction
Browse by: Latest US Patents, China's latest patents, Technical Efficacy Thesaurus, Application Domain, Technology Topic, Popular Technical Reports.
© 2024 PatSnap. All rights reserved.Legal|Privacy policy|Modern Slavery Act Transparency Statement|Sitemap|About US| Contact US: help@patsnap.com