Crane brake control method and system
A brake control, crane technology, applied in the direction of transportation and packaging, load hanging components, safety devices, etc., can solve the problems of cranes lacking fault protection measures, prone to slipping hooks, and safety hazards of slipping hooks, etc., to achieve perfect fault protection The effect of the measures
- Summary
- Abstract
- Description
- Claims
- Application Information
AI Technical Summary
Problems solved by technology
Method used
Image
Examples
Embodiment Construction
[0029] In order to facilitate the understanding of the present invention, the present invention will be described more fully below with reference to the associated drawings. Preferred embodiments of the invention are shown in the accompanying drawings. However, the present invention can be embodied in many different forms and is not limited to the embodiments described herein. On the contrary, these embodiments are provided to make the understanding of the disclosure of the present invention more thorough and comprehensive.
[0030] The following provides a braking control method and system for a crane, which changes the output frequency of the frequency converter and controls the opening or closing of the brake according to the different states of the frequency converter and the received instructions, and continuously obtains the output current and output speed of the frequency converter. Torque, as well as real-time acquisition of brake status feedback, ensure that the inve...
PUM
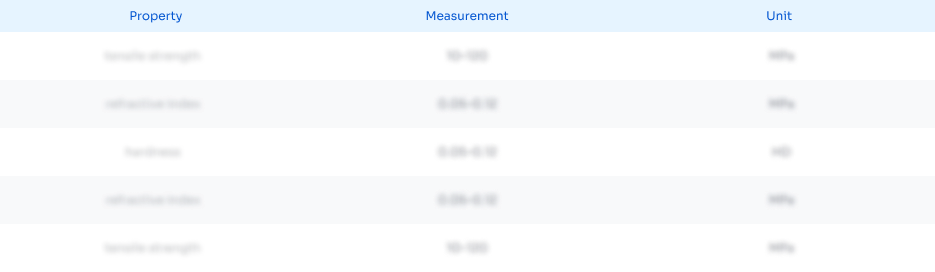
Abstract
Description
Claims
Application Information

- R&D
- Intellectual Property
- Life Sciences
- Materials
- Tech Scout
- Unparalleled Data Quality
- Higher Quality Content
- 60% Fewer Hallucinations
Browse by: Latest US Patents, China's latest patents, Technical Efficacy Thesaurus, Application Domain, Technology Topic, Popular Technical Reports.
© 2025 PatSnap. All rights reserved.Legal|Privacy policy|Modern Slavery Act Transparency Statement|Sitemap|About US| Contact US: help@patsnap.com