Sine driving method of permanent magnet synchronous motor
A technology of permanent magnet synchronous motor and driving method, applied in motor control, AC motor control, electrical components, etc.
- Summary
- Abstract
- Description
- Claims
- Application Information
AI Technical Summary
Problems solved by technology
Method used
Image
Examples
Embodiment Construction
[0021] In order to make the object, technical solution and advantages of the present invention clearer, the present invention will be further described in detail below in conjunction with the accompanying drawings and embodiments. It should be understood that the specific embodiments described here are only used to explain the present invention, not to limit the present invention.
[0022] Such as figure 1 As shown, there are 3 linear Hall sensors evenly arranged around the motor with a difference of 120 degrees. The linear Hall sensor detects the three-phase analog signal as the original static Hall signal:
[0023]
[0024] However, the original static Hall signal has amplitude error and DC error. Among them, θ is the angular displacement of the rotor relative to the Hall sensor, A n and D n (n=1, 2, 3) are respectively the amplitude gain and the DC component of the nth Hall signal, which can be obtained by measurement.
[0025] pass: Convert the three-phase analog ...
PUM
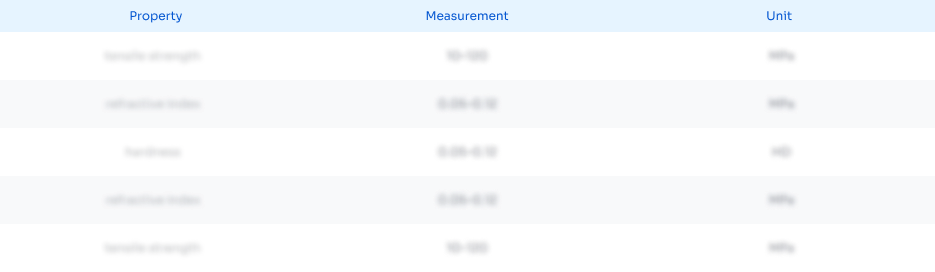
Abstract
Description
Claims
Application Information

- Generate Ideas
- Intellectual Property
- Life Sciences
- Materials
- Tech Scout
- Unparalleled Data Quality
- Higher Quality Content
- 60% Fewer Hallucinations
Browse by: Latest US Patents, China's latest patents, Technical Efficacy Thesaurus, Application Domain, Technology Topic, Popular Technical Reports.
© 2025 PatSnap. All rights reserved.Legal|Privacy policy|Modern Slavery Act Transparency Statement|Sitemap|About US| Contact US: help@patsnap.com