Material crushing cavity structure and design method of multi-stage nested type material crushing cavity structure
A material crushing and design method technology, applied in the direction of computing, grain processing, special data processing applications, etc., can solve problems such as low efficiency, wear, and lack of consideration
- Summary
- Abstract
- Description
- Claims
- Application Information
AI Technical Summary
Problems solved by technology
Method used
Image
Examples
Embodiment 1
[0099] The invention provides a crushing chamber structure with different sizes, shapes and structures and different distribution positions, which are combined into a multi-level nested laminated crushing geometric cavity according to certain requirements. On the one hand, materials with different particle sizes can be collected. On the other hand, the crushing load can be homogenized along the height direction of the crushing cavity, thereby improving the crushing efficiency and prolonging the service life of the liner.
[0100] A material crushing chamber structure, comprising:
[0101] The material inlet is used to import the input material having the characteristics of the first material;
[0102]The first crushing cavity structure is connected with the material inlet, the first crushing cavity structure is used to crush the input material, and the first crushing cavity structure has a first crushing structure that matches the characteristics of the first material. A cavi...
Embodiment 2
[0163] Based on embodiment 1, further, there are:
[0164] 1. If figure 1 The design steps of the primary crushing chamber shown are as follows:
[0165] (1) The working surface of the fixed cone liner 1 is made up of several steps, and the concave-convex inner conical surface between each adjacent step, the value of the conical surface length between the number of steps, height and steps and The particle size distribution of the feed is related to the crushing efficiency.
[0166] (2) The working surface of the movable cone liner 2 is made up of several steps, and the concave-convex outer conical surface between each adjacent step. The number of steps on the working surface of the cone liner 1 corresponds to the spacing between the steps.
[0167] (3) The upper area 31, the middle area 32, and the lower area 33 of the primary crushing cavity are formed between the steps on the working surface of the fixed cone liner 1 and the movable cone liner 2, and the bite angle of eac...
PUM
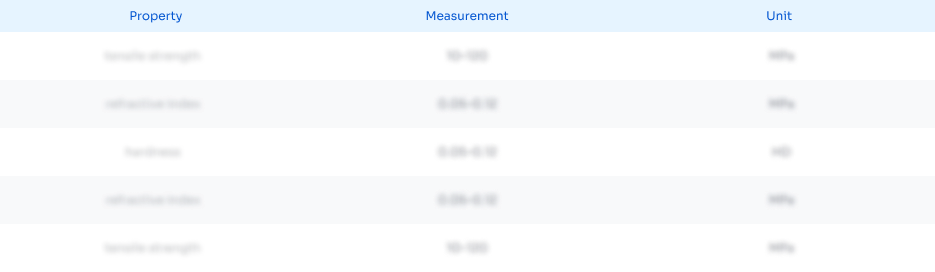
Abstract
Description
Claims
Application Information

- Generate Ideas
- Intellectual Property
- Life Sciences
- Materials
- Tech Scout
- Unparalleled Data Quality
- Higher Quality Content
- 60% Fewer Hallucinations
Browse by: Latest US Patents, China's latest patents, Technical Efficacy Thesaurus, Application Domain, Technology Topic, Popular Technical Reports.
© 2025 PatSnap. All rights reserved.Legal|Privacy policy|Modern Slavery Act Transparency Statement|Sitemap|About US| Contact US: help@patsnap.com