Optimizing method for measuring point spacing of array element position calibration in underwater acoustic positioning navigation system
A technology of array element position and navigation system, which is applied to radio wave measurement systems, instruments, etc., to achieve the effect of improving calibration accuracy and eliminating model mismatch errors
- Summary
- Abstract
- Description
- Claims
- Application Information
AI Technical Summary
Problems solved by technology
Method used
Image
Examples
specific Embodiment 1
Specific embodiment one:
[0044] The present invention provides a method for optimizing the distance between array element position calibration and measurement points of an underwater acoustic positioning navigation system. The method includes the following steps:
[0045] Step 1: According to the measurement position coordinates of the survey ship, establish an optimization model for accurate calibration of the array element position;
[0046] Step 2: Establish the relationship between the time delay measurement error and the sending and receiving distance function;
[0047] Step 3: Construct the error transfer function of the array element position calibration delay measurement, use the differential evolution algorithm to solve the element position calibration delay measurement error transfer function, and obtain the position result and error of the array element to be measured;
[0048] Step 4: Use statistical methods to obtain the calibration accuracy of the array element...
specific Embodiment 2
[0071] To sum up, the process flow of the accurate calibration of the array element position and the optimization of the measurement point spacing of the underwater acoustic positioning navigation system designed by the present invention is as follows: figure 1 shown.
[0073] Firstly, the relationship between the delay measurement error of 10.5kHz and 11.5kHz signals and the distance between sending and receiving is given, as shown in figure 2 and image 3 shown. It can be seen from the figure that the delay measurement error increases with the increase of the transmitting and receiving distance, and the signal delay measurement error increases rapidly with the increase of the transmitting and receiving distance in the first 2000m, and then the growth trend tends to be flat.
PUM
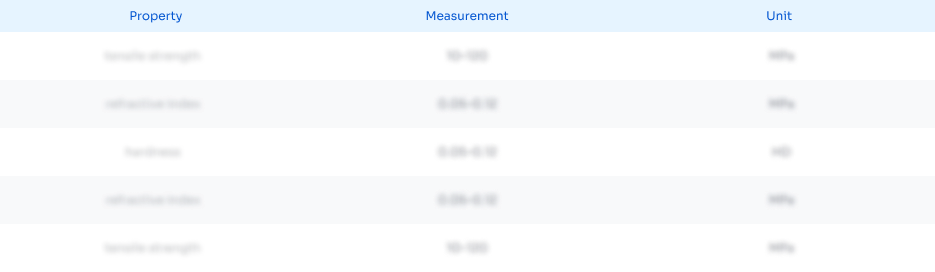
Abstract
Description
Claims
Application Information

- R&D
- Intellectual Property
- Life Sciences
- Materials
- Tech Scout
- Unparalleled Data Quality
- Higher Quality Content
- 60% Fewer Hallucinations
Browse by: Latest US Patents, China's latest patents, Technical Efficacy Thesaurus, Application Domain, Technology Topic, Popular Technical Reports.
© 2025 PatSnap. All rights reserved.Legal|Privacy policy|Modern Slavery Act Transparency Statement|Sitemap|About US| Contact US: help@patsnap.com