A Step-by-Step Machining Method of Extra-long Turnout Point Rail
A processing method and step-by-step technology, which is applied in the field of rail processing, can solve problems such as long strokes of machine tools, and achieve the effect of reducing equipment investment costs
- Summary
- Abstract
- Description
- Claims
- Application Information
AI Technical Summary
Problems solved by technology
Method used
Image
Examples
Embodiment 1
[0028] The super-long point rails of high-speed turnouts are made of special AT rails rolled into standard rail shapes by heel end. The front part is processed by cutting, and the section changes slowly; the rear part is a relatively complete section of AT rail and standard rail, and is processed by driving surface line (rail top and working side). With the gradual widening and heightening of the section size, the contact point gradually shifts from the basic rail to the tip rail when the wheel passes. Schematic diagram of the structure of the super long point rail of the turnout figure 1 shown.
[0029] The following takes CN42# switch point rail as an example to introduce the typical parts and mainstream methods of super-long switch point rail processing. The main structure of other types of point rails is similar. CN42# turnout tip rail processing mainly includes rail bottom milling, rail bottom hole drilling and reaming, rail waist drilling, non-working side rail head mi...
PUM
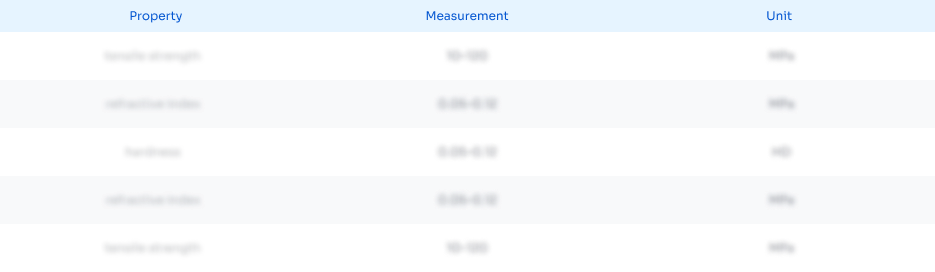
Abstract
Description
Claims
Application Information

- R&D Engineer
- R&D Manager
- IP Professional
- Industry Leading Data Capabilities
- Powerful AI technology
- Patent DNA Extraction
Browse by: Latest US Patents, China's latest patents, Technical Efficacy Thesaurus, Application Domain, Technology Topic, Popular Technical Reports.
© 2024 PatSnap. All rights reserved.Legal|Privacy policy|Modern Slavery Act Transparency Statement|Sitemap|About US| Contact US: help@patsnap.com