Production equipment used for automatic snap-fit of dome assemblies
A production equipment and automatic buckle technology, applied in metal processing equipment, metal processing, manufacturing tools, etc., can solve problems such as excessive deformation of shrapnel, uneven quality, skin and epidermis damage, etc., to achieve accurate positioning, reliable action, and high efficiency. high effect
- Summary
- Abstract
- Description
- Claims
- Application Information
AI Technical Summary
Problems solved by technology
Method used
Image
Examples
Embodiment 1
[0031] refer to Figure 1 to Figure 3 , this embodiment discloses a production equipment for automatic fastening of shrapnel components, which has a body 5, and the body 5 is provided with a pushing mechanism, a first clamping tool and a second clamping tool, and the first The clamping tool is provided with a first clamping end adapted to one end of the lower conductive sheet 2 away from the connection point of the energy storage elastic piece 201 and a second clamping end adapted to one end of the lower conductive sheet 2 close to the connection point of the energy storage elastic piece 201. The clamping end, the horizontal height of the first clamping end is higher than the second clamping end, so as to tilt it when clamping the lower conductive sheet 2, and the first clamping end is provided with the upper conductive sheet 1 The second clamping tool is located above the second clamping end, and is used to fix the upper conductive sheet 1 above the lower conductive sheet 2 w...
Embodiment 2
[0050] This embodiment takes Embodiment 1 as the main body, and its main difference is that the production equipment in this embodiment also includes a detection mechanism 12 for detecting whether the upper conductive sheet 1 and the lower conductive sheet 2 are fully engaged. Such as Figure 10 As shown, the detection mechanism 12 is located on the right side of the push rod 4, and the distance between the detection mechanism 12 and the push rod 4 is equal to the distance between the push rod 4 and the end of the channel 3, so as to facilitate the work of the pushing actuator.
[0051]Correspondingly, the body 5 is provided with two discharge ports at the end of the channel 3, and a flap is arranged between the two discharge ports, and the flap is driven by a cylinder or a motor so that the two discharge ports can be separated. Butt channel 3 ends. In this way, when the detection mechanism 12 detects whether the upper conductive sheet 1 and the lower conductive sheet 2 are f...
Embodiment 3
[0053] This embodiment takes Embodiment 1 as the main body, and its main difference is that the gripper 1103 in this embodiment is directly set at the end of the upper conductive sheet trough 1001, so that the upper conductive sheet 1 is directly sent into the gripper through the second vibrating mechanism 1002 Inside 1103. Afterwards, the upper conductive sheet 1 is directly inserted into the channel 3 through the jaws 1103 . In this embodiment, the introduction mechanism 11 does not need to be provided with a first pushing mechanism and a second pushing mechanism, and the structure is simpler.
PUM
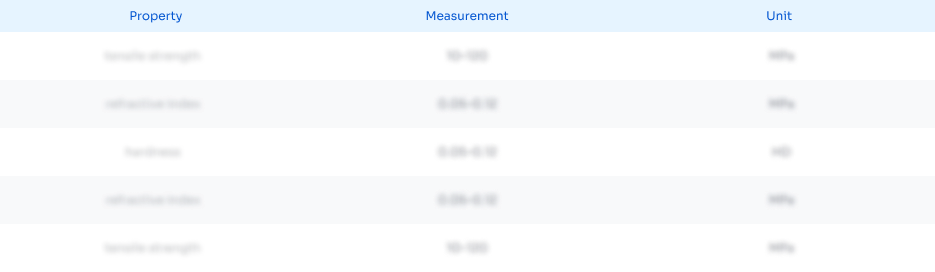
Abstract
Description
Claims
Application Information

- R&D Engineer
- R&D Manager
- IP Professional
- Industry Leading Data Capabilities
- Powerful AI technology
- Patent DNA Extraction
Browse by: Latest US Patents, China's latest patents, Technical Efficacy Thesaurus, Application Domain, Technology Topic, Popular Technical Reports.
© 2024 PatSnap. All rights reserved.Legal|Privacy policy|Modern Slavery Act Transparency Statement|Sitemap|About US| Contact US: help@patsnap.com