Thin film assembly for photovoltaic solar cell lamination
A technology of solar cells and thin-film modules, applied in the field of solar cells, can solve problems such as inability to fix solar cells and poor stability, and achieve the effects of not being loose, improving stability, and ensuring normal operation
- Summary
- Abstract
- Description
- Claims
- Application Information
AI Technical Summary
Problems solved by technology
Method used
Image
Examples
Embodiment 1
[0021] see Figure 1-3 , in an embodiment of the present invention, a thin film assembly for photovoltaic solar cell lamination, comprising a lower glass layer 1, a lower PVB thin film layer 3, a mounting groove 4 and an upper PVB thin film layer 7, the upper surface of the lower glass layer 1 A buffer layer 2 is laid, and the material of the buffer layer 2 is silica gel, and the buffer layer 2 is used to play a buffering role. The upper surface of the buffer layer 2 is laid with a lower PVB film layer 3, and the upper surface of the lower PVB film layer 3 is processed with installation recesses. Groove 4, bus bar installation groove 6, the solar cell is placed in the installation groove 4, and the bottom of the installation groove 4 is processed with anti-slip protrusions 5, which play a role in anti-skid, so that the solar cell remains stable, and the bus bar is installed in the In the bus bar installation groove 6, the bottom of the bus bar installation groove 6 is processe...
Embodiment 2
[0024] A thin film assembly for photovoltaic solar cell lamination, comprising a lower glass layer 1, a lower PVB thin film layer 3, an installation groove 4 and an upper PVB thin film layer 7, the upper surface of the lower glass layer 1 is laid with a buffer layer 2, the buffer layer The material of layer 2 is silica gel, and the buffer layer 2 is used for buffering. The upper surface of the buffer layer 2 is laid with a lower PVB film layer 3, and the upper surface of the lower PVB film layer 3 is processed with installation grooves 4 and bus bar installation grooves. 6. The solar cell is placed in the installation groove 4, and the bottom of the installation groove 4 is processed with anti-slip protrusions 5, which play an anti-skid role and keep the solar cell stable. The bus bar is installed in the bus bar installation groove 6, The bottom of the bus bar installation groove 6 is processed into an arc shape, which is convenient for installation. The upper surface of the lo...
PUM
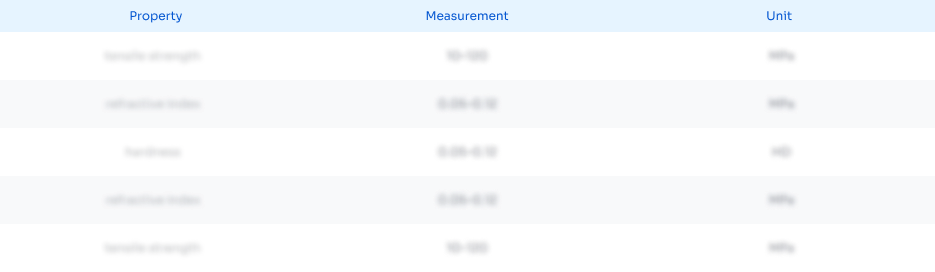
Abstract
Description
Claims
Application Information

- R&D Engineer
- R&D Manager
- IP Professional
- Industry Leading Data Capabilities
- Powerful AI technology
- Patent DNA Extraction
Browse by: Latest US Patents, China's latest patents, Technical Efficacy Thesaurus, Application Domain, Technology Topic, Popular Technical Reports.
© 2024 PatSnap. All rights reserved.Legal|Privacy policy|Modern Slavery Act Transparency Statement|Sitemap|About US| Contact US: help@patsnap.com