Preparing method of exhaust way
A technology for exhaust ducts and molds, which is applied to manufacturing tools, ceramic molding machines, etc., can solve problems such as high noise, pockmarked exhaust ducts, and mold deformation, so as to reduce equipment damage, increase service life, and reduce vibration frequency. Effect
- Summary
- Abstract
- Description
- Claims
- Application Information
AI Technical Summary
Problems solved by technology
Method used
Image
Examples
Embodiment 1
[0070] Embodiment 1 (tilted vibration mode one)
[0071] Such as figure 1 As shown in -8, a method for preparing an exhaust duct, after the mold is positioned, the following process is performed:
[0072] Pouring of the first stage of slurry:
[0073] The slurry is poured in the top area L4 of the mold, the fluid slurry flows into the first side area L1 and the second side area L2, and gathers in the bottom area L3, and the slurry is continuously poured until the slurry is filled to the bottom Area L3;
[0074] Preferably, during the pouring process of the slurry in the first stage, the amount of slurry dispersed into the first side area L1 and the second side area L2 is generally the same or close, and after the slurry fills the bottom area L3, the first There is still a certain amount of slurry in the side area L1 and the second side area L2.
[0075] Wherein, during the pouring process of the slurry in the first stage, the horizontal vibration of the mold may or may n...
Embodiment 2
[0095] Embodiment 2 (tilted vibration mode two)
[0096] Such as Figure 9 -16. A method for preparing an exhaust channel, especially a method for preparing a mechanism exhaust channel. After the mold is positioned, the following process is performed:
[0097] Rotation of the first stage of the mold:
[0098] Rotate the mold around the first direction toward the first side area L5 to an inclined posture, at this time, an inclination β is formed between the bottom area L7 in the casting cavity and the horizontal plane;
[0099] Preferably, the inclination angle β formed between the bottom area L7 in the casting cavity and the horizontal plane is 10°-45°, further, the inclination angle β is about 20°, and the inclination angle β in this embodiment is 15°, Compared with the oblique vibration mode in Embodiment 1, the inclination angle in this embodiment is smaller, and the vibration effect is more prominent.
[0100] Wherein, after the mold rotates to an inclined posture, th...
Embodiment 3
[0121] Embodiment 3 (tilted vibration mode two)
[0122] A method for preparing an exhaust duct. The difference between this embodiment and Embodiment 2 is that: in the tilting vibration stage of the mold, there are also:
[0123] Periodic swinging process of the mold: the mold alternately rotates around the first direction toward or away from the first side area to change the inclination angle formed between the plane of the bottom area in the casting cavity and the horizontal plane, through multiple cycles During the swing process, the gas in the bottom area (including the gas mixed in the slurry in the bottom area) can be completely exhausted, and the air holes and pockmarks on the side wall of the exhaust channel (especially the side wall formed in the bottom area of the casting cavity) can be avoided. .
PUM
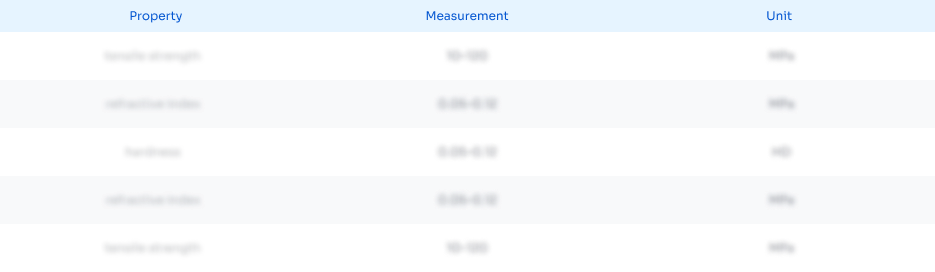
Abstract
Description
Claims
Application Information

- R&D Engineer
- R&D Manager
- IP Professional
- Industry Leading Data Capabilities
- Powerful AI technology
- Patent DNA Extraction
Browse by: Latest US Patents, China's latest patents, Technical Efficacy Thesaurus, Application Domain, Technology Topic, Popular Technical Reports.
© 2024 PatSnap. All rights reserved.Legal|Privacy policy|Modern Slavery Act Transparency Statement|Sitemap|About US| Contact US: help@patsnap.com