Rail robot power driving mechanism and system and rail robot
A rail robot and power-driven technology, applied in the field of robotics, can solve the problems of inconvenient adjustment of driving wheel friction, constant driving energy consumption, poor climbing ability, etc., to improve environmental adaptability, avoid wear, and improve use The effect of longevity
- Summary
- Abstract
- Description
- Claims
- Application Information
AI Technical Summary
Problems solved by technology
Method used
Image
Examples
Embodiment 1
[0028] like figure 1 and figure 2 As shown, the orbital robot power drive mechanism of the present embodiment comprises an orbital walking driving device 1 and a main frame 2, the main frame 2 is provided with a guide wheel assembly 21 and a pair of slide grooves 22, and the two sides of the orbital traveling driving device 1 are provided with There is a connecting column 11 protruding laterally. The connecting column 11 is slidably arranged in the sliding groove 22. A track installation position is formed between the guide wheel assembly 21 and the track running part 12 of the track running drive device 1. One end of the sliding groove 22 is provided with a The connecting column 11 is pressed against the pressure regulating device 23 for adjusting the frictional force of the rail installation position. Since both sides of the track driving device 1 are pressed against the pressure regulating device 23, on the one hand, the pressure regulating device can be adjusted accordin...
Embodiment 2
[0052] In this embodiment, the stroke adjustment assembly is a manual stroke adjustment assembly. Compared with the electric stroke adjustment assembly of Embodiment 1, the manual stroke adjustment assembly is simpler in structure and lower in cost, and it is quite more suitable for a relatively single track structure, such as all tracks 3 with a fixed slope, or all of which are specific arcs shaped structure track 3 and so on. like Figure 8 As shown, the manual stroke adjustment assembly includes a fixed screw sleeve 237, and the fixed screw sleeve 237 is sleeved with an adjusting bolt that is threaded. The adjusting bolt is connected to the spring adjusting plate 233. By rotating the adjusting bolt, the position of the spring adjusting plate 233 / The stroke changes, and then the pressure can be adjusted according to the needs to meet the climbing ability of the ramp or the energy saving of the straight track; it is also possible to use different walking pressures for the i...
PUM
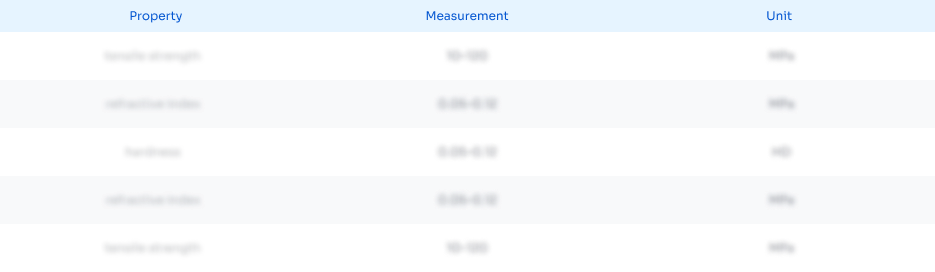
Abstract
Description
Claims
Application Information

- Generate Ideas
- Intellectual Property
- Life Sciences
- Materials
- Tech Scout
- Unparalleled Data Quality
- Higher Quality Content
- 60% Fewer Hallucinations
Browse by: Latest US Patents, China's latest patents, Technical Efficacy Thesaurus, Application Domain, Technology Topic, Popular Technical Reports.
© 2025 PatSnap. All rights reserved.Legal|Privacy policy|Modern Slavery Act Transparency Statement|Sitemap|About US| Contact US: help@patsnap.com