Grinding system and grinding method
A grinding and grinding disc technology, which is applied in the direction of grinding slides, grinding racks, grinding bed, etc., can solve the problems that the workpiece to be ground is not easy to be installed automatically, and the output shaft of the grinding motor is easily damaged due to large force, so as to reduce the The risk of bending, the effect of simplifying the structure and shortening the stroke
- Summary
- Abstract
- Description
- Claims
- Application Information
AI Technical Summary
Problems solved by technology
Method used
Image
Examples
Embodiment 1
[0045] Such as Figure 1-3 As shown, this embodiment provides a grinding system suitable for grinding the inner wall of the object to be ground, including: a frame 1;
[0046] At least one workbench 2 is provided with a fixture 5, the fixture 5 is used for the installation and positioning of the object 6 to be ground, and the workbench 2 is provided with a via hole;
[0047] The grinding disc 4 is suitable for being transported into the inner cavity of the object to be ground 6;
[0048] The rotating main shaft 8 is arranged on the frame 1 in a liftable manner, and the rotating main shaft 8 has a first working position and a standby position, wherein the standby position is a position where the rotating main shaft 8 is under the workbench 2, and the first The working position is the position where the rotating spindle 8 extends upward through the through hole into the inner cavity to install or remove the grinding disc 4;
[0049]The grinding disc automatic installation mech...
Embodiment 2
[0062] The present embodiment provides a kind of grinding method, adopts the grinding system in embodiment 1, comprises the following steps:
[0063] Clamping the object to be ground 6;
[0064] Transport the grinding disc 4 to the inner cavity of the object to be ground 6, and drive the rotating main shaft 8 to pass through the workbench 2 from the standby position and enter the first working position of the inner cavity of the object to be ground 6, and install the grinding disc 4 on the rotating main shaft the upper end of 8;
[0065] Move to the area to be ground for grinding;
[0066] After grinding, return to the first working position for disassembly, and the rotating main shaft 8 descends to the standby position.
[0067] In the above-mentioned grinding method, the object to be ground 6 is positioned and installed by the fixture 5, and the installation method is preferably pneumatic clamping; The installation method is manual or automatic; then press the start butto...
PUM
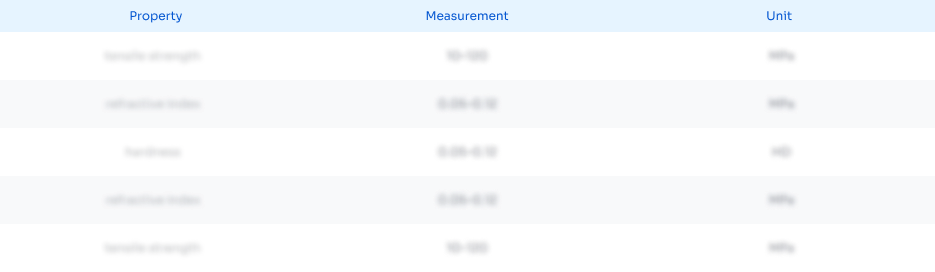
Abstract
Description
Claims
Application Information

- Generate Ideas
- Intellectual Property
- Life Sciences
- Materials
- Tech Scout
- Unparalleled Data Quality
- Higher Quality Content
- 60% Fewer Hallucinations
Browse by: Latest US Patents, China's latest patents, Technical Efficacy Thesaurus, Application Domain, Technology Topic, Popular Technical Reports.
© 2025 PatSnap. All rights reserved.Legal|Privacy policy|Modern Slavery Act Transparency Statement|Sitemap|About US| Contact US: help@patsnap.com